Расчет параметров зубчатого зацепления. Цель работы
Лабораторная работа №21
Построение эвольвентных зубчатых профилей методом обкатки с помощью
учебных приборов, расчет и проектирование зубчатой передачи
Цель работы: изучить теоретические основы нарезания эвольвентных зубчатых колес рейкой методом обкатки и влияние смещения зубчатой рейки на форму нарезаемых колес, изучить методику расчета основных параметров зубчатых колес, изучить методику расчета и проектирования зубчатой передачи, с использованием блокирующего контура.
В настоящее время мы строим машину с несколькими зубчатыми валами, которые приводятся в действие цилиндрическими зубчатыми колесами, но возникают проблемы с определением правильного расстояния между валами. Валы удерживаются подшипниками, установленными на приспособлении. И чтобы следить, как только мы узнаем правильный интервал между центрами и центрами, сколько нужно сопротивления, чтобы удерживать это измерение?
Стейси, спасибо за ваши вопросы. Прежде чем мы ответим на них, мы должны прочитать небольшую справочную информацию для других читателей. Если вы посмотрите на представленную картинку, вы увидите пример двух цилиндрических зубчатых колес со шпоночными канавками, которые могут быть установлены на конце двух валов. Механизмы сидят в «сетчатом» состоянии, что означает, что зубцы шестеренок взаимодействуют друг с другом и что они готовы передать мощность. Хотя может показаться, что все зубчатые передачи созданы равными, существует несколько вариантов «угла давления» зубов, традиционно 5 °, 20 ° и 25 °.
Получение эвольвентных профилейметодом обкатки
Геометрическая форма и размеры зубьев нарезаемого колеса зависят от формы, размеров инструмента и его положения относительно заготовки колеса.
По методу обкатки зубья колес нарезаются (рис.1) долбяками на зубодолбежных станках, гребенками на зубострогальных станках, червячными фрезами на зубофрезерных станках.
Это угол, при котором два противоположных зуба встречаются при зацеплении. Больший угол означает большие зубы и, следовательно, большую прочность и крутящий момент. Однако меньший угол означает меньший зазор, более высокий коэффициент контакта и более плавную и более тихую работу. Независимо от того, какой угол вы выберете, все зубчатые передачи должны иметь одинаковый угол для правильной работы!
Теперь мы рассмотрим вопрос Стейси о расстоянии от вала. Если вы посмотрите на приведенную выше диаграмму, вы увидите «Расстояние по центру», указанное справа. Как правило, диаметр шага для шестерни предоставляется изготовителем, но если вам нужно его вычислить. Тогда центральное расстояние.
Метод обкатки базируется на теории эвольвентного зацепления, основное положение которого заключается в том, что движущемуся инструменту и заготовке сообщаются относительные движения, одинаковые с движениями звеньев соответствующий зубчатой передачи .
Одним из преимуществом этого метода является то, что он позволяет одним и тем же инструментом нарезать зубчатые колеса с любым числом зубьев и различной формы профиля.
Зазор - это зазор или потерянное движение, вызванное зазорами между шестернями. Для предотвращения связывания требуется небольшое количество люфта, но слишком много может привести к чрезмерному шуму или ошибкам позиционирования в валах. Знание требуемого люфта важно, поскольку оно обеспечивает допуск на центральном расстоянии. Независимо от желаемого зазора или типа и размера используемых зубчатых колес, при определении отрицательного допуска следует соблюдать особую осторожность. Если валы расположены слишком близко друг к другу, это может вызвать помехи и привязку передач, что может привести к преждевременному износу или катастрофическому сбою.
В процессе обкатки заготовки колеса инструментом происходит перекатывание без скольжения делительной окружности нарезаемого колеса по любой прямой исходного контура инструмента, параллельной его делительной прямой .
Рис.1
Делительной прямой инструмента является прямая, по которой толщина его зуба равна ширине впадины .
Для среднего приложения, тонкий станок. Мощность может передаваться от одного дерева к другому с помощью ремней, колес с трением, зубчатых колес или цепей. Когда соотношение между скоростями должно быть постоянным, применяются зубчатые колеса. Очевидно, что любая пара поверхностей, которые катятся вместе в режиме чистого качения, чтобы обеспечить желаемое соотношение скоростей, может служить основой для конструкции зубчатой передачи. Движение, передаваемое парой хорошо спроектированных зубчатых колес, идентично движению кривых или основных поверхностей, прокатающихся один над другим.
Положение инструмента относительно заготовки нарезаемого колеса определяется его смещением ( xm ) исходного производящего контура , за которое принято кратчайшее расстояние между делительнойной окружностью нарезаемого колеса и делительной прямой номинальной исходной производящей рейки (инструмента) . Здесь x – коэффициент смещения инструмента – отношение смещения к модулю нарезаемого зубчатого колеса; m – расчетный модуль (или просто модуль) цилиндрического зубчатого колеса, равный делительному нормальному модулю, за который принята линейная величина в π раз меньшая нормального шага зубьев, являющегося кратчайшим расстоянием между одноименными профилями соседних зубьев, замеренным по делительной окружности колеса (размерность модуля в мм).
Для того, чтобы пара кривых могла двигаться одна на другую с чистым движением качения, точка касания кривых всегда должна лежать на линии, соединяющей центры вращения кривых. Профессор Камю был идеей взаимозаменяемости зубчатых колес, а Роберт Уиллис, профессор в Кембридже, стал первым практическим применением эпициклоиды, которое будет использоваться при строительстве серии сменных передач. Точно так же из первых математиков была идея использования эвольвентной окружности в профиле зуба, а также для Уиллиса практические реализации.
Первое практическое применение зуба в инволюции было вызвано швейцарским Леонардом Эйлером. Уиллису приписывают создание дантиста его имени для упрощенного контура эвольвентного профиля зуба. Шамбон, Лион, был создателем машины для скошения конических зубчатых колес с помощью фрезерования.
Можно нарезать три вида зубчатых колес методом обкатки (рис.2):
Рис.2
1) колеса без смещения ( x =0), полученные при перекатывании делительной окружности нарезаемого колеса по делительной прямой исходного контура инструмента;
2) колеса с положительным смещением (центральная часть рис.2), полученные при обкатки делительной окружности по прямой, параллельной делительной прямой и отстоящей от нее на величину положительного смещения + xm (инструмент как бы удаляется от центра заготовки x >0);
Существует множество разнообразных форм и размеров снаряжения: от самых маленьких, используемых в часовом производстве и научных приборов до крупных, используемых, например, в снижении скорости паровых турбин судов, в движении печи и мельницы цементных заводов и т.д. область применения передач практически не ограничена. Мы находим их на электростанциях, гидроэлектростанциях и в наземных транспортных элементах: локомотивах, автомобилях, грузовиках, автомобилях, морском транспорте всех видов, самолётах, в черной металлургии: прокатных станов, транспортеров и т.д. шахты и верфи, цементные заводы, краны, вилочные погрузчики, станки, текстильные, пищевые, швейные и обувные машины, химическую и фармацевтическую промышленность и т.д. для самых простых ручных приводов.
3) колеса с отрицательным смещением ( x <0), полученные аналогично, но при отрицательном смещении - xm (инструмент как бы приближается к центру заготовки).
Наименьшее расстояние между центром заготовки и делительной прямой исходного контура инструмента лимитируется отсутствием подрезания зубьев нарезаемого колеса. При подрезании часть эвольвентного профиля у основания зуба нарезаемого колеса срезается в результате интерференции зубьев при станочном зацеплении (рис.3).
Все это большое разнообразие применений шестерни можно сказать, что его единственной целью является передача вращения или вращения с одной оси на другую, уменьшение или увеличение скорости первого, составляющие так называемые «редукторы или множители» скорость и изменения скорости. Очень интересным разнообразием всех этих механизмов являются так называемые «эпициклические поезда» и «дифференциалы».
Поскольку изогнутая форма профилей зубов является эвольвентной или циклоидальной, движение, передаваемое парой звездочек, является чистой прокаткой. Кроме того, отношение вращений с угловой скоростью передаточных шестерен равномерно. По этой причине он применяется в качестве редуктора или множителя в машинах, в которых требуется определенная скорость, и которые не имеют изменений или колебаний скорости. Передачи обеспечивают большую передачу мощности от оси источника питания к другой оси, расположенной на определенном расстоянии, и должны выполнять работу без потери энергии. Механизмы имеют тот недостаток, что они не могут передавать мощность между большими расстояниями между центрами для этих случаев используются шкивы или цепи. Механизмы имеют высокую стоимость по сравнению с другими цепными приводами и шкивами. Механизмы обеспечивают машины с использованием градаций скоростей вращения. . Профиль зуба или форма его боков состоит из двух эвольвентных кривых круга, симметричных относительно оси, проходящей через центр зуба.
Другой дефект зуба при станочном зацеплении, связанный с явлением интерференции, заключается в срезании зуба. Срезание зуба – это срезание части номинальной поверхности у вершины зуба обрабатываемого колеса в результате интерференции зубьев при станочном зацеплении.
Как известно, существует также циклоидальный профиль, хотя он вряд ли используется, за исключением часового дела. Он называется «круговой эвольвент» к кривой, описываемой точкой на линии, которая вращается без скольжения по окружности. Часть профиля зуба, которая находится ниже основания основания, больше не «эвольвентна».
На рисунке двенадцать одинаковых частей, что облегчает компоновку, совпадают с 30 ° и 60 ° чертежных блоков. С конца каждого радиуса рисуется касательная. Обратите внимание, что длины касательных растут в арифметической прогрессии. Кривая, определяемая последовательностью прослеживаемых дуг, с достаточной аппроксимацией является эвольвентной. Естественно, чем меньше деления, сделанные в базовой окружности, тем больше будет аппроксимация кривой, полученной для эвольвенты.
Рис.3
Минимальная величина коэффициента смещения x min для реечного исходного контура, обеспечивающая отсутствие подрезания зуба, определяется по формуле:
где x min – коэффициент наименьшего смещения исходного контура; h a * - коэффициент высоты головки зуба исходного контура инструмента; z min – наименьшее число зубьев свободное от подрезания; z – число зубьев нарезаемого колеса
Как уже было сказано, происхождение непроизвольных состояний, составляющих боковые стороны зубов, находится в «базовой окружности». Угол, который образует линию действия и горизонтальную касательную к примитивной окружности в примитивной точке, представляет собой «угол давления».
Формула, которая дает нам диаметр основания или диаметра основания, выглядит следующим образом. Исходная окружность или окружность основания относится к независимому колесу или шестерне. В настоящий момент эта часть становится частью шестерни, рождается понятие «примитивных рабочих окружностей», которые являются окружностями, которые касаются друг друга и перекатываются над другим без скольжения. Они важны для зубчатых колес, скорректированных при работе с шестерней с расстоянием между центрами, отличными от нормального.
где - угол профиля зуба рейки.
Максимальная величина смещения исходного контура инструмента ограничивается заострением вершин зубьев нарезаемого колеса. Считается, что имеет место заострение если (рис.3), для тяжело нагруженных передач - .
В обычных, примитивы генерации и примитивы операции одинаковы. Угол, при котором в точке профиля касательная в этой точке пересекается, соответствующий векторный радиус называется углом инерции. Угол падения в примитивной точке 1 должен быть равен углу давления.
Полярное уравнение эвольвентное. Из приведенного выше рисунка также следует. Преимущества системы регенерируемого профиля. Экономика процесса высечки. В системе циклоидальной, боковая стенка образована двумя кривыми и, таким образом, преимущество первого хода с точки зрения простоты обработки, не вызывает сомнений.
Основные элементы зубчатой передачи
Зубчатая передача – трехзвенный механизм, в котором два подвижных звена являются зубчатыми колесами, образующими с неподвижным звеном вращательную или поступательную пару .
Рис.4
Механизмы с эвольвентными зубцами являются единственными, которые могут работать с расстояниями между переменными центрами, сохраняя равномерную угловую скорость. Зуб с эвольвентным профилем более твердый, с равным шагом, чем циклоидальный. В зубчатых передачах с циклоидным профилем контакт осуществляется между выпуклыми и вогнутыми поверхностями, а в эвольвентном контакте находится между выпуклыми поверхностями или между выпуклой и плоской поверхностями.
Можно показать, что в эвольвентной системе отношение угловых скоростей остается постоянным, в пределах действия, независимо от того, касаются ли первичные круги; но для передачи постоянного отношения скоростей с циклоидальными шестернями первичные круги должны оставаться касательными.
К основным параметрам, характеризующим зубчатую передачу (рис.4), относятся: межосевая линия, межосевое расстояние a w , полюс зацепления, линия зацепления, угол зацепления , дуга зацепления.
Межосевая линия О 1 О 2 – прямая линия, пересекающая оси зубчатых колес передачи под прямым углом.
Межосевое расстояние a w -расстояние между осями зубчатых колес передачи по межосевой линии.
И в качестве недостатков профиля в непротиворечивости следует отметить. Давление на подшипники, которые имеют тенденцию отделять два элемента, колесо и шестерню. Однако это также происходит в циклоидальном профиле, за исключением случаев, когда контакт между сопряженными зубами встречается в примитиве.
Сшитые поверхности на обоих зубах выпуклые, за исключением внутренних зубов. Таким образом, смазка циклоидных зубов несколько эффективнее, чем у эвольвентных зубов, и это свойство полезно в передачах червяком, который передает важные нагрузки. Согласно относительной ситуации деревьев.
Линия зацепления N 1 N 2 - траектория общей точки контакта зубьев при ее движении относительно неподвижного звена зубчатой передачи , которая при линейном контакте определяется в ее главном сечении . g – длина линии зацепления.
Полюс зацепления зубчатой передачи – точка касания начальных поверхностей зубчатых колес передачи. Определяется как точка пересечения межосевой линии и линии зацепления.
Наиболее используемым является тот, который основан на относительной ситуации валов или валов, на которых установлены шестерни, и чье вращение движения они передают. Винтовые бесконечные, винтовые, конические гипоидные силы. Оси, которые пересекаются под любым углом. Геликоидальные.
- Параллельные оси в одной плоскости.
- Конусообразные, конически-спиральные или спиральные углы.
- Валы, которые разрезаны в одной плоскости.
- Конусная, спиральная и коническая спираль.
- Оси, пересекающиеся перпендикулярно.
Активная линия зацепления В 1 В 2 – часть линии зацепления зубчатой передачи, соответствующая активной действующей линии зуба или, при линейном контакте, активным профилям взаимодействующих зубьев в главном сечении зубчатой передачи , g a - длина активной линии зацепления.
Длина дополюсной части активной линии зацепления g f – длина части активной линии зацепления, соответствующая углу дополюсного перекрытия зубчатого колеса эвольвентной передачи.
Длина заполюсной части активной линии зацепления g a – длина части активной линии зацепления, соответствующая углу заполюсного перекрытия зубчатого колеса эвольвентной передачи.
N 1 , N 2 , B 1 , B 2 – предельные точки линий зацепления и ее активной части. Предельная точка линии зацепления – это каждая из точек, ограничивающих линию зацепления зубчатой передачи и соответствующих предельным точкам действующей теоретической поверхности зуба, которая при линейном контакте является точкой пересечения линии зацепления с предельной линией поверхности зацепления.
Угол зацепления – острый угол в главном сечении эвольвентной цилиндрической зубчатой передачи между линией зацепления и прямой, перпендикулярной к линии центров.
Рабочий профиль зуба – это профиль зуба, расположенный на его рабочей стороне . Рабочая сторона зуба – это боковая поверхность зуба, участвующая в передаче движения . Но в зацеплении участвует не весь эвольвентный, т.е. теоретический рабочий профиль, а только часть его, которая называется активным профилем. Активный профиль зуба – эта часть профиля зуба, соответствующая его активной поверхности. Активная поверхность - часть боковой поверхности зуба, по которой происходит взаимодействие с боковой поверхностью зуба парного зубчатого колеса (т.е. находящееся с ним в зацеплении). mn , ef – фактические рабочие профили зубьев, где m , f – верхние точки активного профиля. Верхняя точка активного профиля – это точка активного профиля, наиболее близкая к его вершине. n , e – нижние точки активного профиля. Нижняя точка активного профиля – это точка активного профиля, наиболее близкая к его переходной кривой.
Дугой зацепления cd называется расстояние между рабочим профилем зуба одного колеса, входящего в зацепление в т. В 1 и выходящего из него в т. В 2 , измеренное по дуге окружности. Дуга зацепления может быть отмечена по любой окружности: начальной, делительной, основной.
Начальная окружность делит зубья на начальную головку и начальную ножку.
Высота начальной головки зуба h wa – расстояние между окружностью вершин зубьев и начальной окружностью цилиндрического зубчатого колеса. Высота начальной ножки зуба колеса h wf – расстояние между начальной окружностью и окружностью впадин цилиндрического зубчатого колеса. Высота зуба колеса h – расстояние между окружностями вершин и падин цилиндрического зубчатого колеса .
Радиальным зазором с называется расстояние между окружностью вершин одного колеса и окружностью впадин другого колеса :
где m – модуль в мм ; – коэффициент радиального зазора.
Воспринимаемое смещение ym - разность межосевого расстояния цилиндрической зубчатой передачи со смещением и ее делительного межосевого расстояния
где а w о – делительное межосевое расстояние , равное полусумме делительных диаметров зубчатых колес при внешнем зацеплении и полуразности при внутреннем зацеплении ; y – коэффициент воспринимаемого смещения, равный отношению воспринимаемого смещения к расчетному модулю цилиндрического зубчатого колеса.
Иначе говоря, воспринимаемое смещение – это расстояние между делительными окружностями колес, измеренное по линии центров.
Коэффициентом перекрытия учитывает непрерывность и плавность работы зубчатого зацепления. Коэффициент перекрытия выражается отношением длины дуги зацепления ( T b , T w , T ) по какой – либо окружности (основной, начальной или делительной) к шагу ( p b , p w , p ) по той же окружности.
Если дуга зацепления меньше шага (), то зацепление будет прерывистым, с повторяющимися ударами в момент входа очередной пары зубьев в зацепление. При дуге зацепления равной шагу () зацепление можно считать непрерывным только теоретически. Нормально работающая передача должна иметь . Для зацепления с прямыми зубьями при и теоретическим пределом является значение
Краткие сведения о зубчатых передачах со смещением
Зубья передач со смещением изготавливают на тех же станках и тем же стандартным инструментом, что и зубья передач без смещения.
Разница заключается в том, что при изготовлении зубчатых колес со смещением инструмент устанавливают с некоторым смещением в радиальном направлении (рис.2 и рис.3). Соответственно, заготовки колес со смещением выполняют с измененным диаметром.
Смещение инструмента определяется по формуле:
где – коэффициент смещения; m – модуль изготавливаемого зубчатого колеса.
На рис.3 показаны зубья, изготавливаемые одним и тем же инструментом, но с различными коэффициентами смещения. Из рисунка видно, что чем больше значение коэффициента смещения, тем профиль зуба более далеко отстоит от основной окружности. При этом уменьшается кривизна эвольвентного профиля и зуб у основания утолщается, а у вершины заостряется.
При колесо превращается в рейку, и зуб приобретает прямолинейные очертания. С уменьшением z уменьшается толщина зуба у основания и вершины, а также увеличивается кривизна эвольвентного профиля. Если число зубьев z достигает некоторого предельного значения z min , то при нарезании зубьев инструментом реечного типа происходит подрезание ножек зубьев. В результате этого значительно снижается прочность зуба на изгиб. По границе подрезания устанавливается минимально допустимое число зубьев. При нарезании прямых зубьев эвольвентного зацепления стандартным инструментом реечного типа минимально допустимое число зубьев, определенное по формуле (2), z min =17.
Как выше отмечалось устранить подрез зубьев при z < z min можно за счет положительного смещения при нарезании зубатых колес.
Необходимо также помнить, что при большом числе зубьев смещение малоэффективно, так как форма зуба при этом почти не изменяется (у рейки и смещение совершенно не изменяет форму зуба).
Смещение инструмента при нарезании цилиндрических зубчатых колес используется также для вписывания передачи в заданное межосевое расстояние.
Блокирующие контуры
Необдуманный выбор численных значений коэффициентов смещения при проектировании зубчатой передачи может привести к следующим дефектам зубьев колес и зубчатого зацепления.
1. Интерференции зубьев - явление, состоящее в том, что при рассмотрении теоретической картины зубчатого зацеления часть пространства оказывается одновременно занятой двумя взаимодействующими зубьями .
2. Уменьшению коэффициента перекрытия и переходу за предельное значение . Для прямозубых передач рекомендуется , для косозубых .
3. Заострению зубьев и переходу за предельное значение S a =0, где S a – толщина зубьев по окружности выступов. Наименьшая предельно допустимая толщина зуба по окружности выступов колес для тяжело нагруженных передач: при поверхностном упрочнении зубьев равна 0,4 m ; для колес с однородной структурой материала зубьев – 0,3 m (рис.5).
4. Подрезанию зубьев (рис.5).
Рис.5
При проектировании зубчатой передачи составленной из колес с числами зубьев z 1 и z 2 и модулем m проектирование зубчатого зацепления сводится к выбору коэффициентов смещения х 1 и х 2 зубчатых колес.
Наиболее удобно рассматривать ограничения, накладываемые на х 1 и х 2 , в системе координат, где по оси абсцисс откладываются значения коэффициента смещения х 1 а по оси ординат х 2 (рис.6). Предельным значениям каждого из перечисленных выше 4-х факторов в этой системе координат соответствует определенная линия, отделяющая зону допустимых значений х 1 и х 2 от зоны недопустимых.
Линии блокирующего контура (см. рис.6):
1 – линия коэффициента перекрытия block );
2 – линия коэффициента перекрытия (фиолетовая линия на рисунке, получаемом при работе с программой block );
Рис.6. Блокирующий контур
3 – линия толщины зуба шестерни (шестерней называют колесо передачи, имеющее меньшее число зубьев) по окружности выступов (зеленые линии на рисунке, получаемом при работе с программой block );
4 – линия толщины зуба шестерни по окружности выступов ;
5 – граница интерференции на ножке зуба колеса (желтые линии на рисунке, получаемом при работе с программой block );
6 – граница интерференции на ножке зуба шестерни (желтые линии на рисунке, получаемом при работе с программой block );
7 – линии минимальной величины коэффициента смещения х 1 при изготовлении шестерни из условия отсутствия подреза зубьев (красная линия на рисунке, получаемом при работе с программой block );
8 – линии минимальной величины коэффициента смещения х 2 при изготовлении колеса из условия отсутствия подреза зубьев (красная линия на рисунке, получаемом при работе с программой block );
9 – изолиния заданного межосевого расстояния а w (голубая линия на рисунке, получаемом при работе с программой block ); при межосевом расстоянии, равном делительному а w о , изолиния 9 проходит через начало системы координат.
Таким образом, блокирующий контур представляет собой область допустимых значений коэффициентов смещения х 1 и х 2 , при которых обеспечивается благоприятные условия зацепления колес : отсутствие подрезания и интерференции, обеспечение требуемого коэффициента перекрытия, отсутствие заострения и т.д.
Зона внутри контура, выделенного на рис.6 штриховкой, определяет область допустимых значений х 1 и х 2 , и является блокирующим контуром.
Оборудование
Прибор ТММ-42 для вычерчивания эвольвентных профилей методом обкатки, бумажный круг («заготовка») из ватмана, чертежный карандаш, циркуль, масштабная линейка, лист кальки (формат А4), программы ” Spurgear ” и « Blo с k ».
Чтобы изучить влияние смещения инструмента на форму профиля зуба и выявить условия, обеспечивающие отсутствие его подрезания, работу проводим на приборе ТММ-42, имитирующем метод обкатки. Общий вид прибора представлен на рис.7.
Рис.7
На основании 1 прибора установлены диск 2 и рейка 3, имитирующая инструмент для изготовления зубчатого колеса. Диск состоит из двух частей: верхней части 2, выполненной из органического стекла и представляющей собой круг с диаметром, равным диаметру заготовки колеса, и нижней части 4 – круга с диаметром, равным диаметру делительной окружности. Оба круга жестко соединены между собой и могут вращаться на оси, укрепленной в основании прибора. Рейка закреплена винтами 5. По бокам рейки размещены две шкалы 6 и 7, а на рейке имеются две риски (справа и слева), служащие для отсчета смещения xm (мм).
Если исходный контур инструмента располагается так, что его делительная прямая m – m касается делительной окружности заготовки, то на последней получим профили зубьев колеса без смещения. Риски на рейке 3 будут совпадать с нулевыми отметками шкал 6 и 7.
При смещении исходного контура инструмента относительно прямой m – m можно получить профили зубьев колес с положительным или отрицательным смещением. Перемещение рейки отсчитывается по шкалам 6 и 7, после чего она фиксируется винтами 5.
Прерывистое поступательное перемещение рейки осуществляется клавишей 8. При нажатии клавиши 8 рабочей собачкой храпового механизма рейка 3 подается влево (по стрелке) на 4 – 5 мм.
Рядом с клавишей 8 находится Г – образная рукоятка 9 свободного хода каретки. В правом положении (рукоятка лежит на упорном штифте) обеспечивается нормальная работа клавиши 8 (т.е. шаговое поступательное перемещение рейки); при повороте рукоятки против часовой стрелки каретка с рейкой перемещается свободно от руки вправо и влево.
Перемещение рейки 3 и поворот диска 2 согласуются при помощи натянутой струны. Чтобы повернуть диск для установки в определенное положение, струну нужно ослабить. Для этого рукоятку 10 прибора нужно повернуть против часовой стрелки. Для натяжения струны рукоятку 10 ставят в положение верхнего упора.
Порядок выполнения работы
Преподаватель указывает студенту номер зубчатой передачи (см. таблицу) для которой необходимо вычертить зубчатые колеса и провести расчет и проектирование зубчатого зацепления.
Таблица данных для лабораторной работы №3
Зубчатой передачи |
Числа зубьев колес передачи |
Модули зубчатых колес мм |
a w , мм |
|||
№ прибора для получе-ния профи-лей зубьев |
z 2 |
№ прибора для получе-ния профилей зубьев |
||||
10 * |
В таблице * отмечены предпочтительные варианты передачи.
I этап. Вычерчивание эвольвентных профилей зубьев при нулевом смещении инструмента методом обкатки (огибания).
1. Ознакомиться с устройством прибора ТММ – 42 и его работой, опробовать механизм передвижения рейки.
2. В отчет по лабораторной работе записать номер прибора (прибор выбирается по таблице в зависимости от номера зубчатой передачи) и заданные величины: модуль (m ), угол профиля рейки (), коэффициент высоты головки зуба (), диаметр делительной окружности ( d ).
3. Вычислить параметры колеса без смещения:
число зубьев колеса z = d / m ;
диаметр основной окружности
шаг по делительной окружности
шаг по основной окружности
толщина зуба по делительной окружности
толщина зуба по основной
окружности
где
.
4. Отвинтив винт 12, снять крышку 11, за ней снять и бумажный круг, имитирующий заготовку колеса.
На заготовке провести циркулем делительную и основную окружности (центр заготовки отмечен проколом тонкой иглы). Установить заготовку на прежнее место.
Установить рейку, чтобы риски на рейке были против нулевых делений шкал.
5. Бумажный круг наложить на три иглы диска 2 и прижать крышкой2, предварительно отвинченной винтом 12.
6. Поворотом рукоятки 9 против часовой стрелки освободить рейку от храпового механизма и перевести ее в крайнее правое положение. Затем обеспечить рабочее состояние рейки, повернув ту же рукоятку 9 до упорного штифта.
7. Обвести карандашом на бумажном круге контур профилей зубьев рейки.
8. Нажимом на клавишу 8 передвинуть рейку влево на один шаг и вновь обвести контур зубьев рейки. Так делается до тех пор, пока рейка не дойдет влево до упора и на бумажном круге получиться 2-3 хорошо вычерченных зуба колеса.
II . этап. Расчет и проектирование зубчатой передачи.
1. Определить по формуле (1) делительное межосевое расстояние заданной преподавателем зубчатой передачи .
Выбрать из ряда R a 40 нормальных линейных размеров численное значение начального межосевого расстояния а w , причем а w >а w о и является ближайшим к нему.
2. Используя программу ” Spurgear ” определить для заданного модуля какие пары чисел зубьев колес z 1 и z 2 возможны при выбранном начальном межосевом расстоянии а w .
Убедиться, что колеса с заданными z 1 и z 2 среди них встречаются. В противном случае изменить межосевое расстояние. Если подобрать начальное межосевое расстояние не удается, то перейти к п.3, взяв значение а w из таблицы №3.
3. Для заданного а w , m , z 1 и z 2 с помощью программы « Block » построить блокирующий контур и определить коэффициенты смещения х 1 и х 2 .
Если числа зубьев z 1 и z 2 одинаковы, то и коэффициенты смещения х 1 и х 2 также должны быть одинаковы.
Выбрать х 1 и х 2 с помощью полученного блокирующего контура.
4. Вычертить эвольвентные профили зубьев с выбранным положительным смещением на учебном приборе ТММ – 42, имеющем, указанный в таблице данных номер.
5. Освободив винты 5, рейку отодвинуть от оси заготовки на величину рассчитанного смещения x 1 m (мм), которое устанавливается по шкалам 6 и 7. Затем рейку вновь закрепить винтами 5.
6. Поворотом рукоятки 10 влево до отказа диск с бумажным кругом освободить и повернуть примерно на 120 0 относительно неподвижной рейки. После этого рукоятку 10 вновь перевести в правое положение, связав общее движение диска 2 и рейки 3.
7. Методом, указанным в пп.7 – 8 (I -го этапа), вычертить три зуба колеса с положительным смещением.
8. Если числа зубьев колес передачи разные z 1 и z 2 , то п. 5 - 7 выполняются и для второго колеса.
9. На изображение зубчатых колес нанести циркулем окружность вершин колеса с положительным смещением. Измерить толщину зуба по окружности вершин и сравнить полученные значения с расчетными .
10. Вычертить зубчатую передачу на карандашной кальке или листе бумаги формата А4 в масштабе 1:1 (рис.1).
11. Провести межосевую линию.
12. На межосевой линии отложить межосевое расстояние О 1 О 2 (а w ), где О 1 – центр шестерни; О 2 – центр колеса.
13. Из центра О 1 провести окружности впадин и вершин шестерни (r f 1 , r a 1 ).
14. Из центра О 2 провести окружности впадин и вершин колеса (r f 2 , r a 2 ).
15. Из центров О 1 и О 2 провести основныеокружности колес ( r в1 , r в2 ).
16. Провести внутреннюю касательную к основным окружностям, отметив на ней точки касания N 1 и N 2 , определяющие линию зацепления длной q .
17. На межосевой линии отметить полюс запления П.
18. Под кальку подложить заготовку, совместить ее центр с центром О 1 . Вокруг этого центра повернуть заготовку так, чтобы один из профилей зуба шестерни с Z 1 совпал с полюсом П. При этом необходимо следить за тем, чтобы линия зацепления была нормалью к профилю зуба. В этом положении зуб шестерни копируется карандашом на кальку.
19. Центр заготовки колеса совместить с центром О 2 , к точке П подвести профиль зуба колеса с Z 2 так, чтобы он вошел в сцепление с зубом шестерни. Зубья колеса с Z 2 также копируются карандашом на кальку.
20. Отметить точки пересечения В 1 и В 2 линии зацепления с окружностями вершин колес. Линия В 1 В 2 будет активной линией зацепления длиной q α . Отметить длину q f дополюсной части и длины q a заполюсной частиактивной линии зацепления.
21. Отметить угол зацепления α w .
22. Из центров О 1 и О 2 провести дуги радиусами О 1 В 1 и О 2 В 2 , определяющими фактические рабочие профили зубьев mn и ef .
23. Из центров О 1 и О 2 провести начальные окружности (r w 1 , r w 2 ) обоих колес. Отметить h wa 1 , h wf 1 – высоту начальной головки и ножки зуба колеса без смещения; h wa 2 , h wf 2 – высоту начальной головки и ножки зуба колес с положительным смещением.
24. Отметить радиальный зазор С.
25. Построить дугу зацепления cd : с началом (точка В 1 ) и концом (точка В 2) зацепления совмещается один из профилей зубьев колеса с положительным смещением и копируется на кальку. Отметить точки пересечения с и d этого профиля с основной окружностью. Дуга cd будет дугой зацепления по основной окружности.
26. Вычислить и занести в отчет и на чертеж зубчатой передачи коэффициент перекрытия:
где В 1 В 2 – длина активной линии зацепления ; p в – шаг зубьев по основной окружности.
1. Все результаты работы занести в отчет лабораторных работ. Вычерченную схему зубчатой передачи и заготовки на чертежной бумаги приложить к отчету.
Контрольные вопросы
1. Что называют модулем зацепления?
2. Что такое производящий исходный контур?
3. Что называют окружностями: делительной, основной, вершин, впадин, начальной?
4. В чем состоит явление подрезания зубьев и каковы критерии подреза?
5. В чем состоит явление заострения зубьев и каковы критерии заострения?
6. Что называется коэффициентом смещения и смещением исходного производящего контура?
7. Что такое коэффициент наименьшего смещения?
8. Что называется эвольвентой?
9. Назовите свойства эвольвенты.
10. Для любой точки эвольвенты показать радиус кривизны и текущий радиус- вектор.
11. Для любой точки эвольвенты показать профильный угол и эвольвентный угол.
12. Что такое полюс зацепления, линия зацепления, угол зацепления?
13. Что такое активная линия зацепления?
14. Покажите на рисунке зубчатой передачи радиальный зазор, чему он равен.
15. Прикладная механика Детали машин Строительная механика
Силы взаимодействия зубьев принято определять в полюсе зацепления. Распределенную по контактной площадке нагрузку в зацеплении заменяют равнодействующей F n , нормальной к поверхности зуба. Эту силу удобно представить в виде составляющих F t, F r , F а.
Окружная сила F t = 2 10 3 Т/d ;
Осевая сила F a = F t tgβ
На ведомом колесе направление окружной силы F t совпадает с направлением вращения, на ведущем – противоположно ему.
Радиальная сила F r = F R tgα = F t tgα / cosβ
Векторы радиальных сил у колес с внешним зацеплением направлены к оси, а у колес с внутренним зацеплением – от оси зубчатого колеса.
2. Расчет прямозубых цилиндрических передач на контактную прочность.
Контактная прочность зубьев является основным критерием большинства зубчатых передач.
В передачах без смещения a w = (d 2 ± d 1)/2 = d 1 (u ± 1)/2
Откуда d 1 = 2 a w /(u ± 1) d 2 = 2a w u/(u ± 1),
где u = d 2 /d 1 – передаточное число передачи.
Наибольшее контактное напряжение в зоне зацепления определяют по формуле Герца:
ν 1,2 – коэффициенты Пауссона материалов контактирующих тел;
Е 1,2 – модули упругости материалов;
ρ 1,2 – радиусы кривизны контактирующих поверхностей;
b – длина линии контакта (длина цилиндров)
Силу F n определяют по окружной силе с учетом коэффициента нагрузки. По результатам экспериментов для расчетов суммарную длину
b= l Σ контактных линий определяют с учетом коэффициента торцевого перекрытия: F n = K H ·Ft/cosα ; b = l Σ = 3b 2 /(4 - ε α).
Контакт зубьев рассматривают как контакт двух цилиндров с радиусами кривизны профилей зубьев в полюсе зацепления:
Подставим полученные значения в формулу Герца:
Σ(1/ρ i)
= 1/ρ 1 ±
1/ρ 2
= (ρ 2
± ρ 1)/(ρ 2 ρ 1)
=
Обозначим:
Z E
=
- коэффициент, учитывающий упругие
свойства материалов сопряженных колес;
Z E
= 191.6 МПа 0,5
для стальных колес при Е 1
= Е 2
= 2,1 10 5 МПа
и ν 1
= ν 2
= 0,3.
Z H
=
- коэффициент, учитывающий форму
сопряженных поверхностей зубьев в
полюсе зацепления; Z H
= 2.5 при α w
= 20 о.
Z ε
=
- коэффициент, учитывающий суммарную
длину контактных линий; Z ε
= 0.9 для прямозубых колес при ε α
= 1,6.
При
этом получим расчетную зависимость в
форме предусмотренной стандартом:
;
Заменив в формуле F t = 2 10 3 Т 1 /d 1 ; b 2 = ψ bа а w ; d 1 = 2а w /(u ± 1) , последовательно получим
Решив
относительно а w
получим а w
=
;
Обозначив
К а
=
Формула
проектировочного расчета цилиндрических
зубчатых передач имеет вид: а w = К а
В соответствии со стандартом:
для прямозубых передач К а = 450 МПа 1/3 ;
для косозубых и шевронных передач К а = 410 МПа 1/3 .
В целом межосевое расстояние косозубой цилиндрической зубчатой передачи примерно на 20% меньше межосевого расстояния прямозубой передачи.
При расчете цилиндрических передач значение коэффициента ширины зубчатого венца колеса ψ ва = b 2 /а w задают. В зависимости от расположения шестерни относительно опор принимают: ψ ва = 0,2 …0,5.
Формула для проверочного расчета:
Значения коэффициента Z σ для цилиндрических стальных передач:
прямозубых Z σ = 9600 МПа 1/2 ;
косозубых и шевронных Z σ = 8400 МПа 1/2
При проектировочном расчете значение коэффициента расчетной нагрузки К Н = 1,3 – задают ориентировочно. При проверочном расчете определяют его уточненное значение по известным размерам и степени точности передачи.
При выполнении проверочного расчета желательно достижение равенства σ Н = [σ] Н , так как при σ Н > [σ] Н – возможно занижение ресурса передачи, а при σ Н < [σ] Н завышение ее массы. Простейшим способом достижения σ Н = [σ] Н является изменение ширины зубчатого венца b 2 . Контактная прочность зубьев колес зависит от материала и размеров передачи и не зависит от модуля и числа зубьев в отдельности. По условиям контактной прочности при данном а w модуль и числа зубьев могут иметь различные значения, но с соблюдением условий: 0,5m(Z 1 + Z 2) = а w и u = Z 2 /Z 1 .
3.Расчет зубьев цилиндрических передач на прочность при изгибе .
Вторым из двух основных критериев работоспособности зубчатых передач является прочность зубьев при изгибе. При выводе расчетной зависимости принимают допущения:
В зацеплении находится одна пара зубьев.
Зуб рассматривают как консольную балку, нагруженную сосредоточенной силой F n , приложенной к зубу в его вершине
Сила F n действует под углом (90 – α /) к оси симметрии зуба; угол α / несколько больше угла зацепления α w . Для выявления напряженного состояния зуба силу F n переносят вдоль линииN 1 N 2 зацепления до пересечения с осью зуба в т. С. и раскладывают на составляющие, направленные вдоль оси зуба и перпендикулярно ей (рис. 2).
Под действием составляющей, направленной вдоль оси, в основании зуба действуют напряжения сжатия σ сж = F n sinα / /bS, эпюра которых показана на рис.3 (b- длина зуба). Точки А и В определяют положение опасного сечения зуба при изгибе. Зуб в этом сечении нагружен изгибающим моментом М = F n h р cosα / , вызывающим действие напряжений σ и: слева от оси – растяжения, справа – сжатия. Суммарные напряжения σ Fном со стороны растянутых волокон (т.А) имеют меньшие значения, чем со стороны сжатых (т.В). Однако напряжения растяжения являются более опасными. Напряжения, наеденные без учета концентраторов, называют номинальными.
Определим номинальные напряжения изгиба – сжатия в т.А:
где W x = bS 2 /6 - осевой момент сопротивления опасного сечения АВ.
Выразив силу F n через окружную силу F t с учетом коэффициента нагрузки K F , получим:
, где F n
= K F F t /cosα w
Опасное сечение АВ расположено в зоне концентрации напряжений, вызванной изменением формы на переходной поверхности в основании зуба. Местное напряжение в этом сечении превышают номинальные в α Т раз:
σ F = σ F ном α Т, где α Т – теоретический коэффициент концентрации напряжений.
С учетом этого напряжения в опасном сечении
Плечо изгиба h p и толщину зуба S выражают через модуль m
где
- коэффициент, учитывающий форму зуба
и концентрацию напряжений. Выбирается
по таблице или графику.
Учитывая условие прочности σ F < [σ] F , получим формулу для проверочного расчета зубчатых передач по напряжениям изгиба:
,
где Y β – коэффициент, учитывающий угол наклона зуба Y β = 1 – β/100, при условии Y β > 0.7; Yε - коэффициент, учитывающий перекрытие зубьев Y ε = 1/ε α = 1/1,6 = 0,65.
Для прямозубых зубчатых колес : Y β = 1; Y ε = 1 при степени точности 8,9;
Y ε = 0,8 при степени точности 5, 6, 7. Y FS 1 > Y FS 2 так как зуб шестерни у основания более тонкий, чем зуб колеса. Для обеспечения примерно равной изгибной прочности сопряженных зубьев шестерню изготавливают из более прочного материала. Условие равной прочности на изгиб зубьев шестерни и колеса: [σ] F 1 /Y FS 1 ~ [σ] F 2 /Y FS 2
Заменив
F t
= 2 10 3 T 1 /d 1
u
d 1
= 2a w /(u
± 1), получим формулу для проверочного
расчета зубьев по напряжениям изгиб и
решим полученное неравенство относительно
m:
Ширину b 1 венца шестерни выполняют на 2 – 4 мм больше ширины b 2 колеса для компенсации возможного осевого смещения зубчатых колес из-за неточности сборки. Это важно при приработке зубьев, когда более твердая шестерня перекрывает по ширине менее твердое колесо.
Приняв b = b 2 и обозначив K m = 10 3 Y FS Y β Y ε , получим расчетную зависимость для определения минимального значения модуля зубьев
m
,
где К m = 3.4 10 3 – для прямозубых передач;
K m = 2.8 10 3 – для косозубых передач.
Вместо [σ] F в формулу подставляют меньшее из [σ] F 1 u [σ] F 2 .
Особенности геометрии и условий работы косозубых передач
Ось червячной фрезы, при нарезании зубьев косозубой цилиндрической передачи, составляет с торцевой плоскостью колеса угол β. Поэтому в нормальной к направлению зуба плоскости все его размеры – стандартные. У косозубого колеса расстояние между зубьями можно измерить в торцевом или окружном, (t – t) и нормальном (n – n) направлениях. В первом случае получают окружной шаг p t , во втором – нормальный шаг p. Различны в этих направлениях и модули зацепления:
m t = p t /π , m n = p / π , где m t ; m n – окружной и нормальный модули.
p t = p / cosβ , следовательно, m t = m n / cosβ . Нормальный модуль должен соответствовать стандарту.
Для колеса без смещения делительный d и начальный d w диаметры:
d = d w = m t Z = m n Z / cosβ
Помимо торцевого перекрытия в косозубых передачах обеспечено и осевое перекрытие.
Коэффициент осевого перекрытия ε β = b 2 /p x , где p x - осевой шаг, равный расстоянию между одноименными точками двух смежных зубьев, измеренному в направлении оси зубчатого колеса (рис.)
Особенности геометрии определяют отличия условий работы косозубой передачи.
1. Зуб ведомого колеса входит в зацепление, начиная с вершины, вначале увеличивая, а затем уменьшая длину контактной линии при перемещении ее от головки зуба, к ножке. Зуб работает не сразу всей длиной, он лучше и быстрее прирабатывается.
2.Увеличивается время контакта одной пары зубьев, в течении которого входят в зацепление новые пары зубьев; нагрузка передает большое число контактных линий, что значительно снижает шум и динамические нагрузки. Чем больше угол наклона β линии зуба, тем выше плавность зацепления.
3.Нагрузка по длине контактной линии распределяется пропорционально суммарной жесткости зубьев шестерни и колеса.
4.В косозубой передаче в зацеплении участвуют одновременно 2-3 пары зубьев. Поэтому суммарная длина контактной линии l Σ кос больше (примерно на 30%), чем в прямозубой l Σ прям
l Σ кос = b 2 /(Z 2 ε cosβ b) ; l Σ прям = b 2 /Z 2 ε .
Коэффициент Z ε учитывает суммарную длину контактной линии:
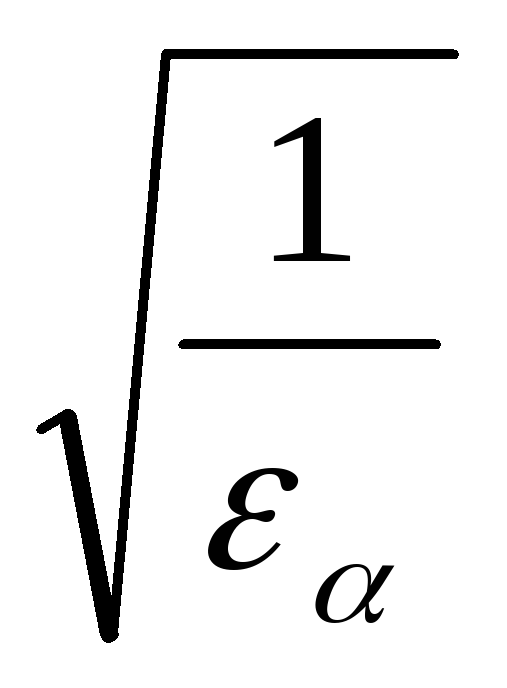
Для прямозубых передач Z ε
=
где ε α – коэффициент торцевого перекрытия.
5.Соотношение между радиусами кривизны контактирующих зубьев в косозубой передаче более благоприятно: Σ(1/ρ і) кос = cosβ b Σ(1/ρ і) прям
Контактные напряжения при прочих равных условиях в косозубом зацеплении меньше по значению, чем в прямозубом.
Понятие об эквивалентном колесе .
Профиль косого зуба в нормальном сечении n – n совпадает с профилем прямозубого колеса. Расчет косозубых колес ведут, используя параметры эквивалентного прямозубого колеса:
m n - модуль; Z v - число зубьев. Профиль зуба совпадает с профилем условного прямозубого колеса, называемого эквивалентным , делительный диаметр d v = m n Z v .
d v = 2ρ v = d/cos 2 β = m t Z/cos 2 β = m n Z/cos 3 β , где ρ v – радиус кривизны.
Из равенства m n Z v = m n Z/cos 3 βследует эквивалентное число зубьев:
Z v = Z/cos 3 β.
C увеличением угла β наклона линии зуба, эквивалентные параметры возрастают, способствуя повышению прочности передачи.
Σ(1/ρ i)
= 1/ρ 1 ±
1/ρ 2
= (ρ 2
± ρ 1)/(ρ 2 ρ 1)
=
Обозначим:
Z E
=
-
Z H
=
Z ε =
;
Заменив в формуле F t = 2 10 3 Т 1 /d 1 ; b 2 = ψ bа а w ; d 1 = 2а w /(u ± 1) , последовательно получим
Решив относительно а w получим
а w
=
;
Обозначив
К а =
а w
= К а
, где
F n
= K F F t /cosα w
h p = μm и S = λm , где μ и λ - коэффициенты, учитывающие форму зуба. Тогда
где
-
, где Y β
m
ПРОЕКТИРОВОЧНЫЙ РАСЧЕТ ЦИЛИНДРИЧЕСКОЙ ПЕРЕДАЧИ
При проектировочном расчете зубчатой передачи удобнее определять не напряжения, а основные геометрические параметры. Межосевое расстояние:
a w
= (u
+ 1)=
, мм
где u - передаточное число;
T 2 - крутящий момент на колесе;
C - коэффициент, учитывающий механические свойства сопряженных зубчатых колес:
310 – для прямозубых цилиндрических передач;
335 – для прямозубых конических передач;
270 – для косозубых цилиндрических и конических передач;
[σ] H - допускаемое контактное напряжение, зависящее от материала и термообработки зубчатых колес и от длительности работы передачи
Зубчатые колеса изготовляют из проката или поковок из качественные конструкционных углеродистых или легированных сталей с содержанием углерода от 0,1 до 9,6% с различными видами термообработки; при значительных размерах колес (диаметром более 500 мм) применяют стальное литье. У прямозубых колес из улучшенных или нормализованных сталей с твердостью не более НВ 350 твердость рабочей поверхности зуба шестерни должна быть на 20 – 50 ед.больше твердости зуба колеса. У не прямозубых колес разность в твердости шестерни и колеса достигает 100 ед.и более, что повышает нагрузочную способность передачи по контактной прочности.
При значительной, но спокойной нагрузке может быть произведена сплошная закалка, при большой и динамической нагрузке внутренняя часть зуба должна быть вязкой, а наружная высокопрочной, при малой динамической нагрузке весь зуб может быть вязким. Если передаваемая мощность большая, то для уменьшения массы и габаритов передачи следует применять колеса с более высокой поверхностной прочностью.т.е. зубья должны иметь сплошную или поверхностную закалку, цементацию, цианирование и … Такие зубья должны шлифоваться или притираться, следовательно степень точности должна быть высокой. Колеса с шевронными зубьями закалке не подвергаются и их шлифовка не производится.
Допускаемые контактные напряжения для шестерни и колеса:
где [σ] Р 0 – допускаемое контактное напряжение, соответствующее базовому числу циклов нагружения N НО (выбирается по таблице 1)
Z R – коэффициент, учитывающий шероховатость рабочих поверхностей зубьев (при 7 классе шероховатости –1; при 6 классе шероховатости – 0,95)
Z V – коэффициент, учитывающий влияние окружной скорости и твердости (определяется по графику Z V – V при твердости НВ≤ 350 и НВ > 350)
К НL
– коэффициент долговечности К Н L
=
где N HO -базовое число циклов нагружения
N HE –эквивалентное число циклов нагружения колеса
N HE
=
где Т i mах – максимальный длительно действующий момент
Т i – моменты в ступенях нагрузки, соответствующие числам циклов нагружения N i (график изменения нагрузки)
N i = 60n i t hi K K(ш)
где n i - частота вращения вала при действии момента Т i , мин -1 ;
t hi - продолжительность действия нагрузки Т i , в часах;
K K – количество зацеплений рассчитываемого колеса.
[σ] Н
=
=
После определения следует проверить выполнение условия:
[σ] Н ≤ 1,23[σ] Н min
С увеличением в сторону увеличения надежности для косозубых передач можно принять значение [σ] Н равным меньшему из двух [σ] Н1 и [σ] Н2
К Нα – коэффициент, учитывающий неравномерность распределения нагрузки между зубьями; для прямозубых колес 1; для косозубых по графику;
К Нβ – коэффициент, учитывающий неравномерность распределения нагрузки по длине контактной линии – определяется по графику или по таблице;
К НV – динамический коэффициент, учитывающий влияние точности передачи, твердости зуба и окружной скорости – определяется по таблице;
Ψ ва – коэффициент ширины зубчатого венца
Ψ ва = b/a w Ψ bd = b/d
Выбор значений ψ ba и ψ bd существенно влияет на качество передачи – ее КПД, габариты, требования к технологии изготовления и сборки; с увеличением коэффициента ширины зубчатого венца повышается концентрация нагрузки При проектировочном расчете величиной ψ ва задаются:
0,125…0,20 – для прямозубых колес коробок передач;
0,20…0,35 – для прямозубых колес редукторов;
0,20…0,50 – для косозубых колес;
0,40…0,80 – для шевронных передач.
Для каждой последующей ступени редуктора ψ ва увеличивается на 20 – 30% по сравнению с предыдущей.
Стандартные значения:0,100; 0,125; 0,160; 0,20; 0,250; 0,315; 0.40; 0,50; 0,630; 0,80; 1.0; 1,25
После определения межосевого расстояния принимают ближайшее стандартное значение: 40; 50; 63; 71; 80; 90; 100; 112; 125; 140; 160; 180; 200; 225; 250; 280; 315; 355; 400; 450; 500; 560; 630.
После корректировки параметров и коэффициентов производится проверочный расчет на контактную выносливость:
σ Н
=
МПа
Здесь в случае, если контактное напряжение не более, чем на 5 …6% превышает допустимое, или недогрузка не превышает 10% то расчет считается удовлетворительным.
Проверка на контактную прочность при кратковременных перегрузках:
σ Н max
= σ H ,
МПа
где [σ] Нпр – предельное напряжение на контактную прочность:
при Н ≤ НВ 350 [σ] Нпр = 3,1σ Т
Н > НВ 350 [σ] Нпр = 41,3НRС
Проверка на выносливость при изгибе:
σ F
=
,
МПа
где Т – крутящий момент на проверяемом колесе, Н.м.
Z – число зубьев проверяемого колеса;
К F α - коэффициент нагрузки, учитывающий распределение нагрузки между зубьями (для прямозубых колес К = 1; для косозубых при среднем коэффициенте торцевого перекрытия ε α = 1,5 и 8 степени точности колес
К Fβ - коэффициент, учитывающий неравномерность распределения нагрузки по ширине венца (таблица)
K FV - коэффициент, учитывающий динамические нагрузки (таблица)
Y F - коэффициент прочности зубьев, определяется по эквивалентному числу зубьев
Z V = Z/cos 3 β
β – угол наклона зуба в косозубых (8 0 … 20 0) и шевронных (25 0 … 40 0) передачах;
Y β - коэффициент, учитывающий наклон зуба, при β< 40 0
Y β = 1 – β/140 0
m - модуль зацепления (для косозубых m n - нормальный модуль)
m = m n = (0,01 … 0,02)a w
Модуль зуба колеса нужно выбирать минимальным так, как с его увеличением растут наружные диаметры заготовок, но не менее1,5 …2 для силовых передач
Определяем числа зубьев колес:
Z 1
=
Z 2
= uZ 1
Минимальное допустимое значение Z 1 , без риска подрезания ножки зуба, для некоррегированных колес: Z min ≥ 17cos 3 β
Допускаемое напряжение при проверочном расчете на выносливость зубьев при изгибе: [σ] F = [σ] F 0 K FL Y R Y M
где [σ] F 0 – допускаемое изгибное напряжение, соответствующее базовому числу циклов перемен напряжений N FO (таблица)
K FL – коэффициент долговечности, зависящий от соотношения базового и эквивалентного чисел циклов нагружений
K FL
=
N FO = 4 10 6 – базовое число циклов
N FE
=
- эквивалентное число циклов при изгибе
m F - степень, m F = 9 – для стальных колес с нешлифованной поверхностью при твердости НВ > 350 и для чугунных колес; m F = 6 – для колес с твердостью менее НВ350
Если N FE > N FO = 4·10 6 то принимаем K FL = 1
Y R – коэффициент, учитывающий шероховатость рабочих поверхностей (1 – для шлифованной и фрезерованной поверхностей; 1.05 – цементация, азотирование; 1,2 – полированная с нормализацией или улучшением)
Y M = 1 при d ≤ 300 – коэффициент, учитывающий диаметр колес.
Определение геометрических параметров цилиндрических колес
Диаметр делительной окружности:
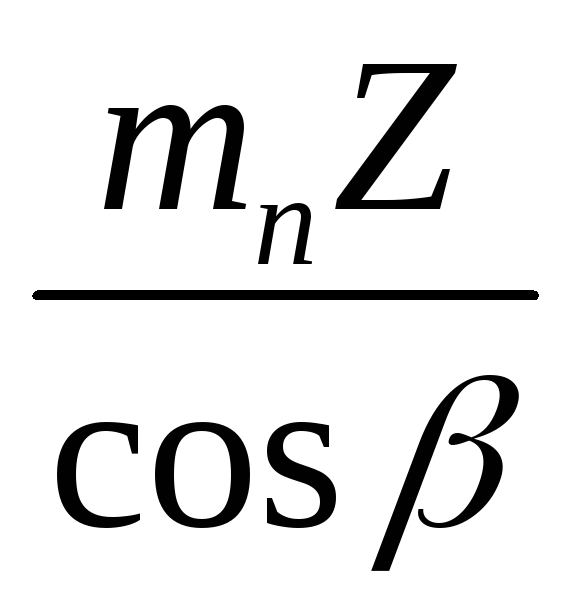
2.Ширина зубчатого венца
для шестерни b 1 = ψ ba ·a w + 5
для колеса b 2 = Ψ ba a w
3.Диаметр вершин зубьев d a = d + 2m n
4. Диаметр впадин d f = d – 2,5m n
5.Окружная
скорость V
=