Цилиндрические редукторы. Классификация мотор редукторов по типу кинематической схемы, вида передач и количества ступеней. Рис.1. Зубчатые редукторы
Мировая промышленность выпускает множество различных типов редукторов. По типу передачи эти редукторы классифицируются на следующие типы:
- цилиндрические
- червячные
- волновые
- гипоидные
- конические
- планетарные
Подробное описание червячных, волновых, цилиндрических, планетарных и конических зубчатых пар.
Червячный мотор-редуктор имеет зубчато-винтовую передачу с линейным контактом. Основными преимуществами червячного редуктора являются большие передаточные числа при меньших габаритах. Червячная передача имеет плавный ход, что позволяет избавиться от шума во время работы мотор-редуктора. Особенность червячной передачи является самоторможение. Мотор-редукторы могут применяться в изделиях, где требуется высокая динамика разгона и остановки, при этом нет обходимости применять дополнительные тормозные устройства. Основная сфера применения червячных редукторов - конвейеры, грузоподъемное оборудование и многие другие области промышленности.
Червячные мотор-редукторы обладают следующими приимуществами:
- реверс выходного вала в обе стороны;
- компактные размеры даже при высоких коэффициентах передаточных чисел;
- плавность хода и низкий уровень шума;
- широкий ряд передаточных чисел;
- передача вращения под прямым углом;
- самоторможение (позволяет быстро остановить выходной вал при снятии питания с клемм электродвигателя);
- доступная цена;
- удобство монтажа.
Цилиндрический мотор-редуктор может применяться для передачи больших мощностей, обладает высоким КПД (более 90%). Цилиндрические мотор-редукторы получили преобладающее распространение в различных отраслях промышленности перед другими видами редукторов. Редукторы данного типа обладают большой долговечностью, имеют компактные размеры и просты в эксплуатации. Скорость вращения выходного вала зависит от передочного отношение, а последнее от количества ступеней передач. Цилиндрические мотор-редукторы имеют, как правило, одну, две или три ступени. Редукторы могут работать в тяжелых условиях в круглосуточном режиме.
Цилиндрические мотор-редукторы обладают следующими приимуществами:
- простая и надежная конструкция;
- вращение тихоходного вала в разные стороны;
- высокие показатели КПД;
- передача больших мощностей;
- удобство монтажа;
- низкая цена.
Волновой мотор-редуктор имеет гибкую механическую передачу. Передача и энергии от электродвигателя до выходного вала происходит за счет деформации гибкого элемента редуктора. Преимуществами волновой передачи являются высокие показатели передаточных чисел и плавность движения. Волновые редукторы могут долго работать на высоких нагрузках без какого либо износа механических пар. Волновые редукторы характеризуются низким уровнем шума и отсутствием нежелательных вибраций во время работы.
Волновые мотор-редукторы обладают следующими приимуществами:
- высокая плавность и точность движений, что позволяет использовать его робототехнике и в точном машиностроении;
- отсутствие вибраций за счет небольшого количества движущихся частей;
- широкий диапазон передаточных чисел;
- большое количество различных вариантов исполнения;
- компактные габариты по сравнению с другими типами механических передач при одинаковой мощности;
- низкий уровень шума
Планетарный мотор-редуктор за счет высоких эксплуатационных характеристик может применяться в силовых приводах, где требуются большой момент и высокие коэффициенты передаточных чисел, при этом габариты и вес будут ниже по сравнению с редукторами другого типа. Как и цилиндрический редуктор, планетарный имеет одну, две или три ступени передачи энергии от двигателя до выходного вала. Конструкция мотор-редуктора имеет соосную схему, т.е. редуктор и электродвигатель располагаются на одной оси. В промышленности России получили широкое распространение мотор-редукторы 3МП, обладающие множеством преимуществ перед редукторами других типов.
Планетарные мотор-редукторы обладают следующими преимуществами:
- вращение выходного вала в разных направлениях без потери рабочих характеристик;
- высокий КПД;
- широкий диапазон передаточных чисел;
- высокая перегрузочная способность даже в тяжелых условиях работы;
- возможность работы с переменной нагрузкой;
- возможность работы в круглосуточном режиме;
- широкий диапазон температурных режимов -40 до +45° С.
Мотор-редуктор конический, цилиндро-конический передает вращение между двумя перпендикулярными валами. В редукторе применяются конические зубчатые передачи с прямым или криволинейным зубом. Редукторы имеют высокий КПД и могут применяться в силовых установках, где требуется высокий момент. Конструкция редуктора простая и не требует трудоемкого обслуживания. Цилиндро-конические редукторы широко применяются в машиностроении, металлургии, строительстве и сельском хозяйстве.
Цилиндро-конические мотор-редукторы обладают следующими преимуществами:
- долговечная работа в течение нескольких лет;
- компактная конструкция;
- широкий диапазон передаточных чисел;
- высокий КПД (не менее 0,94 при любом направлении и скорости вращения);
- валы расположены под прямым углом друг к другу;
- возможность работы с тяжелой нагрузкой и частым старт-стопом.
Классификация мотор редукторов по типу кинематической схемы, вида передач и количества ступеней
Тип редуктора |
Количество ступеней |
Тип механической передачи |
Расположение входного и выходного вала |
Цилиндрический редуктор |
Одноступенчатый |
Одна или несколько цилиндрических передач |
Параллельное |
Параллельное или соосное |
|||
Четырехступенчатый |
Параллельное |
||
Конический редуктор |
Одноступенчатый |
Одна коническая передача |
Пересекающееся |
Коническо-цилиндрический редуктор |
Одна коническая передача и одна или несколько цилиндрических передач |
Пересекающееся или скрещивающееся |
|
Червячный редуктор |
Одноступенчатый; двухступенчатый |
Одна или две червячные передачи |
Скрещивающееся |
Параллельное |
|||
Цилиндрическо-червячный или червячно-цилиндрический редуктор |
Двухступенчатый; трехступенчатый |
Одна или две цилиндрические передачи и одна червячная передача |
Скрещивающееся |
Планетарный редуктор |
Одноступенчатый; двухступенчатый; трехступенчатый |
Каждая ступень состоит из двух центральных зубчатых колес и сателлитов |
|
Цилиндрическо-планетарный редуктор |
Двухступенчатый; трехступенчатый; четырехступенчатый |
Комбинация из одной или нескольких цилиндрических и планетарных передач |
Параллельное или соосное |
Коническо-планетарный редуктор |
Двухступенчатый; трехступенчатый; четырехступенчатый |
Пересекающееся |
|
Червячно-планетарный редуктор |
Двухступенчатый; трехступенчатый; четырехступенчатый |
Комбинация из одной конической и планетарных передач |
Скрещивающееся |
Волновой редуктор |
Одноступенчатый |
Одна волновая передача |
Редуктор | Расположения осей входного и выходного валов в пространстве по типу кинематической схемы |
С пересекающимися осями входного и выходного валов | 1. Горизонтальное |
Со скрещивающимися осями входного и выходного валов | 1. Горизонтальное (с входным валом над или под выходным валом) 2. Горизонтальная ось входного вала и вертикальная ось выходного вала 3. Вертикальная ось входного вала и горизонтальная ось выходного вала |
С совпадающими осями входного и выходного валов (соосный) | 1. Горизонтальное 2. Вертикальное |
С параллельными осями входного и выходного валов | 1. Горизонтальное: оси расположены в горизонтальной плоскости; оси расположены в вертикальной плоскости (с входным валом над или под выходным валом); оси расположены в наклонной плоскости 2. Вертикальное |
Монтажные позиции и способ крепления редукторов
Монтажное крепление |
Монтажное крепление |
Внешний вид |
|
Крепление на монтажных лапах или на плите (к потолку или стене) |
Крепление фланце со стороны входного вала |
||
Монтаж на уровне плоскости основания корпуса редуктора |
Креплени на фланце со стороны выходного вала |
||
Крепление над уровнем плоскости основания корпуса редуктора |
Монтаж на фланце со стороны входного и выходного валов |
||
Крепление с насадкой |
Основные технические характеристики редукторов
Согласно представленным ГОСТам различные виды редукторов имеют ряд характеристик, которые можно разделить на следующие категории:
Рабочий ресурс – определяется количеством часов работы редуктора гарантированный производителем. Для различных типов редукторов этот показатель имеет разные значения. Например, червячная передача имеет гарантированный ресурс не менее 11000 часов, а цилиндрическая и планетарная уже более 26000 часов. Также на условия безотказной работы влияет ресурс подшипников, имеющий обычно интервал времени от 500 часов. Производитель обычно гарантирует безотказную работу редуктора в течении 5-6 лет, при условии, что нет перегрузок.
Допустимые условия эксплуатации :
- Рабочее напряжение и ток. В стандартном исполнение все мотор-редукторы питаются от сети переменного тока напряжением 220/380В. Малогабаритные двигатели с фазосдвигающим конденсатором мощностью до 2,2 кВт можно подключать в однофазную сеть, а двигатели мощностью свыше 2,2 кВт только в трехфазную промышленную сеть напряжение 380В.
- Температура окружающей среды . В стандартном исполнении все мотор-редукторы рассчитаны работать при температуре от -40 до +50ºС, а если же условия работы выходят за рамки температурных режимов, следует сменить смазку на более подходящую.
- Скорость вращения быстроходного вала . Для нормальной работы редуктора скорость вращения входного вала не должна превышать 1800 об/мин.
- Мощность электродвигателя . Подводимая мощность электродвигателя не должна превышать расчетную более 10 %, в противном случае, при увеличении выходной нагрузки, может выйти из строя редукторная часть.
Климатическое исполнение. Определяется в зависимости от местности и климатических условий где будет эксплуатироваться редуктор. Обычно производители определяют условия работы как умеренные, тропические и умеренно-холодные.
КПД редуктора. Данный параметр зависит от типа механической передачи, передаточного отношения и количества ступеней.
Другие характеристики обычно представлены в инструкциях по эксплуатации конкретного редуктора.
Сферы применения мотор-редуктров
Назначение мотор-редуктора - понижение скорости электродвигателя и увеличение момента вращения. В зависимости от поставленных задач редукторы успешно применяются во многих отраслях народного хозяйства. Редукторы просто незаменимы там, где требуется что-то вращать, смешивать, передвигать. Мотор-редукторы с успехом применяются в машиностроении, строительстве, металлургии, при работе в составе ленточных, цепных, роликовых конвейеров, экструдеров, различных подъемных устройств, приводов пил и ножниц, транспортирующих тележек, приводов поворотных механизмов, приводов ходовых винтов. Любая автоматизированная система имеет в качестве привода мотор-редуктор.
Наибольшее распространение получили червячные, цилиндрические, планетарные и конические мотор-редукторы. Все эти редукторы имеют различные варианты крепления и могут комплектоваться специальными электродвигателями со встроенным тормозом или двигателями во взрывозащитном исполнении. Многослойная окраска позволяет эксплуатировать привод на улице под навесом, не опасаясь коррозионных разрушений.
Эксплуатационные коэффициенты и характеристики нагрузки
Эксплуатационные коэффициенты и характеристики нагрузки в таблицах показывают характер нагрузки при различных применениях, что помогает выбрать редуктор, подходящий для определенной задачи. Для выбора модели необходимо использовать фактическую нагрузку, а не характеристики мотора или первичного двигателя. Системы, оснащенные моторами с большим моментом или моторами для прерывистых операций, а также системы с регулярными ударными нагрузками или необходимостью поглощения высоких нагрузок, например при потерях скорости, требуют особого внимания. Системы, связанные с необычными или большими нагрузками, а также системы, требующие высокой надежности, должны быть тщательно изучены инженерным отделом.
Эксплуатационные коэффициенты представляют обычное отношение между номинальной мощностью системы и непрерывно потребляемой мощностью. Как правило, эксплуатационные коэффициенты делятся на равномерные, коэффициенты для средних и высоких нагрузок. Если при установке тормозов на входе двигателя номинальный момент тормоза превышает номинальный момент мотора, редуктор следует выбирать в соответствии с моментом тормоза. Для редких запусков (менее 5 запусков в час) максимальная моментальная или стартовая нагрузка не должна превышать 275 % номинальной (175-процентная перегрузка). Для частого запуска (более 5 запусков в час) фактическая максимальная моментальная или стартовая нагрузка не должна превышать 200 % номинальной (100-процентная перегрузка). Номинальная нагрузка определяется системой с эксплуатационным коэффициентом 1,0. Опубликованная гарантия производителя относится ко всем закрытым приводам, если выполняются указанные ниже условия. Установка защищена от внешнего воздействия, как указано производителем, во внутреннем или внешнем хранилище с момента получения покупателем до момента установки. Система правильно установлена и смазана в соответствии с указаниями производителя.
Используется совместимая система соединенных вращающихся деталей, не достигающая критических скоростей, и не подверженная торсионной или другой вибрации в указанных пределах скорости.
Эксплуатационные коэффициенты
Эксплуатационные коэффициенты используются для изменения номинальной механической мощности. На практике фактическая мощность умножается на выбранный эксплуатационный коэффициент для получения так называемой эквивалентной мощности. Эта эквивалентная (механическая) мощность используется для выбора редуктора из таблиц. Эксплуатационные коэффициенты не применяются к тепловой мощности, только к механической.
Механические показатели
Списки номинальных механических мощностей в таблицах выбора относятся к непрерывной работе на протяжении 8–10 часов и допускают 100-процентную перегрузку при запуске и моментальных нагрузках. Все компоненты рассчитаны на менее чем 5 запусков в час, пиковые нагрузки в 275 % от указанных номиналов с перегрузками, не превышающими 75 % предела текучести материала. Если механический показатель превышает тепловой, можно применять полный механический номинал, при условии принятия соответствующих мер по охлаждению.
Тепловые показатели
Номинальная тепловая мощность - это показатель мощности, непрерывно передаваемой на протяжении 3 или более часов без несвоевременных скачков температуры. Она применяется только если механическая мощность выше тепловой, и не принимались меры по охлаждению. Тепловые показатели следует учитывать, если период непрерывной работы не превышает трех часов, а время отключения больше или равно времени работы. Если время работы превышает время отключения, выбор следует выполнять на основании теплового показателя либо следует принять меры по охлаждению.
Внешние радиальные нагрузки
Если на вал редуктора действует внешняя радиальная нагрузка, найдите подходящую для выбранного редуктора тягу по указанной ниже формуле.
тяга = F x 1 948 000 x кВт / D x об.мин
кВт
- фактическая передаваемая мощность.
об./мин
- количество оборотов вала в минуту.
D
- диаметр ведущей шестерни или шкива на валу в мм.
F
- коэффициент, принимающий следующие значения:
шкив - 1,0 / ведущая шестерня - 1,25 / ремень - 1,5 / плоский ремень - 2,5.
Допустимые радиальные нагрузки рассчитаны для центра удлинений вала
Устройство и принцип работы мотор редуктора
Редуктор и электродвигатель, соединенные в единую конструкцию, называют мотор-редуктором. Мотор-редуктор имеет компактные размеры, обычно его монтаж не вызывает каких любо трудностей. Редуктор состоит из корпуса, куда укладывается червячная, или цилиндрическая, или коническая, или планетарная передача - зависит от типа редуктора. Также в состав редуктора входят валы, подшипники и сальники. Корпус изготавливается из сплава алюминия или чугуна - зависит от назначения и типоразмера редуктора. Сами же передачи обычно состоят из одной или нескольких ступеней, надежно заключенных в подшипники. Материалом передач служит прочная сталь и бронза, последняя из которых применяется только в редукторах червячного типа. Передаточное отношение обычно зависит от количества зубьев соприкасаемых шестеренок, а также от количества ступеней.
Устройство мотор-редуктора достаточно простое. Каждый из типов редукторов имеет различные конструктивные особенности. Так, например цилиндрический мотор-редуктор серии 4МЦ2С представляет собой механизм на базе двухступенчатого редуктора и электродвигателя. Редуктор имеет соосную схему сборки, оси валов двигателя и редуктора расположены в вертикальной плоскости. Ведущая шестерня монтируется непосредственно на вал двигателя и передает энергию на зубчатое колесо, напрессованное на вал шестерню. Вал-шестерня крепится на двух конических подшипниках и передает вращение, находясь в зацеплении с другим зубчатым колесом напрессованным на выходной вал, который вращающается на двух роликовых подшипниках. Цилиндрическая передача имеет косозубое эвольвентное заципление. Выходной вал уплотнен манжетой, а неподвижные соединения прокладками и герметиком. Принцип работы заключается в передаче вращения от вала электродвигателя на первичный вал, далее на блок зубчатых пар, а потом на выходной вал редуктора. Куда более простую конструкцию имеет червячный мотор-редуктор . Момент передается от двигателя на червячный винт, а далее на зубчатое колесо насаженное на выходной вал редуктора. Каждый тип редукторов имеет свои достоинства и недостатки. Например илиндрический мотор редуктор позволяет передавать высокий момент без потерь на трения, а червячный - позволяет передать вращение под прямым углом.
Планетарный мотор редуктор представляет собой устройство, в котором объедены зубчатый планетарный редуктор и электродвигатель. Планетарная передача представляет собой механизм, состоящий из центрального колеса насаженного непосредственно на вал электродвигателя передающего момент на три сателлита установленных на подшипниках. Оси сателлитов запрессованы консольно на водило на длину равную 1,2 диаметра оси. Водило первой ступени и колесо второй ступени выполнены «плавающими», что обеспечивает равномерное распределение момента среди трех сателлитов.
Как правильно выбрать мотор редуктор?
При постановке задачи разработки или модернизации оборудования, где применяется привод, возникает вопрос: "Как правильно выбрать мотор-редуктор?".
Ниже перечислены основные характеристики, влияющие на правильный выбор мотор-редуктора:
- Нагрузка прикладываемая к выходному валу редуктора - крутящий момент M2, [Н м.]
- Скорость вращения выходного вала редуктора n2, [об/мин]
- Режим и время работы - коэффициент эксплуатации Sm
Вышеперечисленные данные помогут определить передаточное отношение i , мощность электродвигателя P1 и типоразмер редуктора.
Выходной крутящий момент Mk можно найти, зная какое усилие F2 действует на определенное расстояние r2 (плечо)
Mk [Нм] = F2 [N] x r2 [м]
Надежная работа мотор-редуктора определяется таким параметром как коэффициент эксплуатации Sm
Динамика разгона с небольшими ударными нагрузками, неравномерная нагрузка во время работы, средняя начальная масса (лебедки, мешалки смесительные, транспортные ленты, лифты, деревообрабатывающие, печатные и текстильные машины)
Тяжелая динамика разгона, сильные удары в процессе работы, высокая начальная масса (компрессоры, молоты, бетономешалки, всасывающие насосы, прокатные станы, гибочные машины и прессы, конвейеры тяжелого груза, машины с переменным движением)
Сервис фактор Sf – это отношение максимально допустимого момента M2 max указанного в паспорте редуктора к номинальному моменту M2 зависящего от мощности электродвигателя.
М2
- момент на валу редуктора - Н/м
n2
- частота вращения вала – об/мин
n
- показатель КПД редуктора - %
Радиальная и осевая нагрузка вала
k
- коэффициент нагрузки
D
- диаметр шкива или шестерни на выходном валу [мм]
M2
- выходной крутящий момент
1,10
звездочка
1,25
шестерня
1,50
ременный шкив
Из вышеуказанной формулы следует, что радиальная нагрузка Fr зависит от диаметра шкива D притом, чем больше диаметр, тем ниже нагрузка.
Осевую нагрузку Fa max можно найти, зная значения радиальной нагрузки Fr .
Fa max [N]
– максимально допустимая осевая нагрузка
Fr [N]
– максимально допустимая радиальная нагрузка
Что такое передаточное отношение и как его определить?
Для подбора аналога вышедшего из строя редуктора требуется ряд параметров, которые можно определить самому без помощи специалистов. Так, например, типоразмер редуктора можно определить померив диаметр выходного вала, аналогично можно определить мощность установленного на редуктор электродвигателя. Передаточное отношение можно определить опытным путем, вращая входной вал до тех пор, пока выходной вал не сделает один полный оборот, при этом не забывая считать обороты входного вала. Соотношение количества оборотов приложенных к входному валу, при которых выходной вал провернется на один полный оборот - и есть передаточное отношение.
Бывает, что редуктор, который нужно заменить аналогом не проворачивается по причине заклинивания зубчатых пар, а бывает наоборот - какая-либо передача износилась, и вращение быстроходного вала не передается к тихоходному валу. В таких случаях поможет методика подсчета количества зубов на шестерне и заходов на винте. Данный метод актуален для червячных редукторов.
В червячном редукторе основными элементами являются зубчатое колесо и червячный винт. Допустим нам нужно определить передаточное отношение редуктора серии Ч125.
Для этого на редукторе нужно снять крышку со стороны выходного вала.
За ней находится зубчатое колесо, на котором нужно подсчитать количество зубов. В нашем случае - 32 зуба.
Получив исходные данные - 32 зуба на колесе и 1 заход на винте, находим передаточное отношение, разделив 32/1.
Основными параметрами редукторов являются тип, типоразмер и исполнение.
Типоразмер редуктора определяет тип и главный размер (параметр) тихоходной ступени.
- Для цилиндрического и червячного редукторов главным параметром является межосевое расстояние a w ,
- Для конического - внешний делительный диаметр колеса d 2 ,
- Для планетарного - радиус водила R.
- Одним из главных параметров редуктора является передаточное число (табл. П9 Приложения).
Параметрами редуктора являются
- коэффициенты ширины колес,
- модули зубчатых колес,
- углы наклона зубьев, а
- для червячного редуктора дополнительно - коэффициент диаметра червяка q.
Основная энергетическая характеристика редуктора - момент на выходном валу
где Р вх - мощность на быстроходном валу; ω вх - угловая скорость быстроходного вала; и - передаточное число редуктора; η - КПД редуктора.
Обозначение редукторов
В обозначении указывается
· число ступеней,
· схема сборки.
Если валы расположены в одной горизонтальной плоскости, в обозначении это не отражается. Если все валы расположены в вертикальной плоскости, в обозначении типа добавляют индекс В, если ось выходного вала вертикальна - добавляют букву Т, если ось быстроходного вала вертикальна - добавляют букву Б.
Цифрами указываются главный размер (параметр) тихоходной ступени и передаточное число редуктора.
Например, изображенный на рис. 14.3, а
редуктор обозначается Ц2-200-4: двухступенчатый цилиндрический редуктор, межосевое расстояние 200 мм, передаточное отношение 4.
Представленный на рис. 14.3, б редуктор обозначается Ч-140-25: червячный редуктор, межосевое расстояние 140 мм, передаточное отношение 25.
Опорами валов в редукторах чаще всего являются подшипники качения. Валы цилиндрических и конических редукторов, как правило, устанавливают на шариковых или роликовых конических подшипниках.
При относительно коротких валах осевая фиксация выполняется на двух опорах: один подшипник фиксирует вал в одном направлении, а другой - в другом (на рис. 14.4 тихоходный вал при указанном направлении силы F a 2 в осевом направлении фиксируется на опоре А, установка враспор). Установка вала на конических подшипниках враспор представлена на рис. 14.5. Таким подшипникам необходима осевая регулировка наружных колец, выполняемая с помощью винта 1.
Осевой зазор в подшипнике может также регулироваться изменением толщины прокладок 1 под крышкой подшипников (см. рис. 14.4). Для крепления коротких валов применяют установку подшипников врастяжку (на рис. 14.6 крепление быстроходного вала). При направлении силы F a , как показано на рис. 14.6, осевая фиксация происходит на опоре А. Стакан 2 используется для регулировки зазора в зацеплении конических колес.
Длинные валы закрепляют от осевых смещений в одной опоре, вторую опору выполняют плавающей (на рис. 14.4 осевая фиксация быстроходного вала на опоре В, опора Г - плавающая; на рис. 14.7 осевая фиксация вала червяка на опоре А, опора Б - плавающая). На плавающей опоре внутреннее кольцо подшипника крепится с обеих сторон уступами вала, пружинными кольцами, распорными втулками.
![]() |
Наружные кольца подшипников крепятся крышками. Крышки подшипников могут приворачиваться к корпусу винтами (рис. 14.6), под крышки помещают прокладки. Используют конструкции с врезными крышками, уступающими по герметичности (см. рис. 14.4, 14.5).
Смазывание редукторов
В редукторах обеспечивается смазывание зубчатых зацеплений и подшипниковых узлов. Масло в корпус заливают через пробки 1 в люках (см. рис. 14.6). Уровень масла контролируется масломерной иглой и с помощью специальных указателей уровня 3. В горизонтальных редукторах тихоходное колесо погружают в масло на половину ширины венца. Иногда используют специальные улавливатели, направляющие масло в пространство между подшипниками шестерни. В вертикальных редукторах обычно достаточно погружения колеса тихоходной ступени.
Уплотняющие устройства
Уплотняющие устройства предохраняют от загрязнения извне и предотвращают вытекание смазочного материала.
Для уплотнения подшипниковых узлов применяют контактные уплотнения - манжеты (см. рис. 14.7, опора Б), щелевые, лабиринтные, (см. рис. 14.4, опора Б).
Применяют также внутренние уплотнения подшипниковых узлов. При смазывании пластичным материалом подшипниковый узел прикрывают мазеудерживающими кольцами.
Глава 15. Муфты
Знать назначение, конструкции муфт основных типов, оценку муфт и области их применения; принцип подбора стандартных и нормализованных муфт и порядок проверки на прочность основных элементов.
Основные функции муфт - соединение валов и передача вращающего момента. Соединяя валы машин, муфты выполняют и ряд дополнительных функций: компенсируют перекосы и смещения валов, смягчают колебания и динамические нагрузки, обеспечивают при необходимости плавные пуски и остановки, предохраняют детали машин от перегрузок и изменения направления вращения.
Классификация муфт
Муфты подразделяют на
Постоянные (глухие, компенсирующие, упругие);
Сцепные управляемые;
самоуправляющиеся (автоматические) по моменту (предохранительные), по направлению движения (обгонные), по скорости (центробежные).
Типы муфт
1. Жесткие некомпенсирующие (глухие) муфты не допускают соединение валов со смещениями или перекосами валов.
Втулочные муфты (рис. 15.1, а) требуют соосности валов. Муфты изготовляют со штифтами и шпоночным пазом. Муфты просты в изготовлении, дешевы, но установка (монтаж) связана с необходимостью больших осевых перемещений валов. Муфты не позволяют посадки деталей с натягом, не обеспечивают жесткость валов.
Фланцевые муфты (рис. 15.1, б) наиболее распространены, в них необходимо обеспечить перпендикулярность торцовых поверхностей А к оси вала.
2. Жесткие компенсирующие муфты допускают соединения валов с незначительным смещением осей.
Особую группу составляют шарнирные муфты , допускающие значительные перекосы осей валов
Широко распространена зубчатая муфта (рис. 15.1, в). Наружная поверхность зубьев втулок муфты сферическая, зубья имеют эвольвентный профиль. Вследствие большого числа зубьев муфты имеют большую несущую способность и надежность. Муфты допускают смещение валов в осевом направлении до 8 мм, в радиальном - до 0,6 мм, перекос - до 1 0 30". Зубчатые муфты используют в широком диапазоне моментов и скоростей вращения, они технологичны и малогабаритны. Основные недостатки - скольжение зубьев и их износ; используется смазывание зубьев.
3. Упругие компенсирующие муфты смягчают толчки и удары, передаваемые через соединяемые валы, предохраняют от колебаний и компенсируют все виды перекосов валов. Муфты содержат неметаллические упругие элементы (из резины) или металлические - пружины, пакеты пластин.
Упругая втулонно-палъцевая муфта (МУВП) (рис. 15.1, г) состоит из двух полумуфт, соединенных через палец с надетыми на него резиновыми втулками. Муфта проста по конструкции, компактна и мала по массе, изнашивающиеся резиновые кольца легко заменяются. Муфты допускают осевые смещения до 5 мм, радиальные смещения - до 0,6 мм, перекосы - до 1°.
4. Сцепные управляемые муфты служат для соединения и рассоединения вращающихся или неподвижных валов. Муфты разделяются на муфты с профильным замыканием (кулачковые и зубчатые) и фрикционные. Муфты с профильным замыканием применяют для передачи значительных вращающих моментов, если не требуется плавность соединения.
Для плавного соединения и рассоединения валов используют фрикционные муфты (рис. 15.1, д - ж). Работа фрикционных муфт основана на создании сил трения между элементами муфты. Силу трения можно регулировать, меняя силу сжатия трущихся поверхностей. Управление муфтой может быть механическим, гидравлическим и электромагнитным. По форме трущихся поверхностей муфты разделяются на дисковые, конусные и цилиндрические. Различают сухие муфты и муфты, работающие со смазкой.
В процессе включения фрикционной муфты происходит проскальзывание, и разгон ведомого вала идет плавно. Муфта регулируется на передачу максимального момента, безопасного для элементов машины.
Для уменьшения габаритных размеров муфту выполняют с несколькими поверхностями трения - многодисковая муфта (см. рис. 15.1, д). Все диски муфты должны быть параллельными, плоскими и соосными, поэтому все диски устанавливают на одной из полумуфт - необходима абсолютная соосность валов.
Достоинствами конусных муфт (см. рис. 15.1, ё) являются малые силы включения, хорошая расцепляемость и простота конструкции. Основные недостатки - большие габаритные размеры и неуравновешенные осевые силы, передаваемые на валы.
В цилиндрической шинно-пневматической муфте (см. рис. 15.1, ж) осевых усилий на вал не создается, допускаются осевые смещения, момент легко регулируется.
Основные недостатки таких муфт - значительная стоимость резинового баллона и нестойкость резины к нефтепродуктам.
5. Сцепные самоуправляющиеся муфты предназначены для сцепления и расцепления валов при изменении заданного режима работы.
Для этого применяют обгонные муфты (свободного хода), передающие момент в одном направлении, центробежные муфты для соединения и рассоединения валов при достижении определенной частоты вращения и предохранительные муфты , выключающие механизм при перегрузках.
По принципу работы предохранительные муфты делят на
· пружинные,
· фрикционные и
· с ломающимся элементом.
По конструкции пружинно-кулачковые и фрикционные подобны сцепным управляемым муфтам.
Из муфт с ломающимся элементом широко распространена фланцевая муфта со срезанным штифтом (рис. 15.1, з). При перегрузке штифт срезается и полумуфты рассоединяются. Такие муфты просты по конструкции, имеют малые размеры, основной недостаток: для замены перерезанного штифта необходимо останавливать машину и заменять штифт.
Параметры часто используемых муфт см. в табл. П25-П27 Приложения.
Цилиндрический редуктор - это одна из самых популярных разновидностей редукторов. Он, как и все редукторы, служит для изменения скорости вращения при передачи вращательного движения от одного вала к другому.
Именно редукторный привод один из наиболее распространенных видов приводов современных механических систем общепромышленного применения. Более ста лет назад перед нашей промышленностью стояла задача обеспечить нужды страны в цилиндрических редукторах. С этим успешно справлялись открывающиеся заводы. В настоящее время выпуск качественной и надежной продукции обеспечивается мощной производственной базой. Сейчас производят различные типы продукцией: цилиндрический редуктор одно-, двух-, и трехступенчатый.
От работоспособности и ресурса цилиндрического редуктора во многом зависит обеспечение требуемых функциональных параметров и надежности машины в целом. Показатели долговечности и надежности элементов привода и, в частности, редукторов и мотор-редукторов, зависят от обоснованного выбора самого редуктора при проектировании машины, т.е. соответствия этого выбора действующей нормативной документации (НД). Неправильный выбор редуктора снижает его рыночную конкурентоспособность, нанося ущерб производителю, и может привести к значительным экономическим потерям потребителя машиностроительной продукции из-за внеплановых простоев, роста ремонтных затрат и пр. Одно из важнейших требований обеспечения конкурентоспособности цилиндрического редуктора - наилучшее соответствие его паспортных характеристик реальным эксплуатационным условиям нагружения и работы привода машины.
Редуктор (от лат. reductor - отводящий назад, приводящий обратно) - это механизм, входящий в приводы машин и служащий для снижения угловых скоростей ведомого вала с целью повышения крутящих моментов. В редукторах применяют зубчатые передачи, цепные передачи, червячные передачи, а также используют их в различных сочетаниях - червячные и зубчатые, цепные и зубчатые и т.п. Существуют комбинированные приводы, в которых редуктор компонуют с вариатором. Редуктор используют в транспортных, грузоподъёмных, обрабатывающих и др. машинах. Главными характеристиками редукторов служат коэффициент полезного действия (КПД), мощность, передаточное отношение, угловые скорости валов, количество ступеней и передач и др.
Ещё в глубокой древности применялся принцип редукторов - увеличение приложенной силы или тяги. Эта идея механической передачи приложенного усилия восходит от изобретения колеса. Каким образом функционирует простая передача? Два колеса соприкасаются с собой ободами. Большое колесо делает оборотов меньше, по сравнению с меньшим. Когда колесо поменьше - становится ведущим, то крутящийся момент передачи получается больше, потеряв в скорости угловой. Для подъемов огромных грузов подобная передача применяется часто. Установив зубчатые колёса вместо гладких, получим передачу тяги и усилия более производительной. Вот так в человеческой жизни начали появляться редукторы. С появлением паровой машины возникла необходимость в передаче еще больших мощностей. Соответственно, потребовалось конструировать металлические редукторы. К 1850 г. ткацкие станки с механическим приводом были уже втрое производительнее ручных станков. Более дешевая энергия дала возможность повысить быстродействие станков, и это укрепило их экономическое преимущество. Паровой двигатель был достаточно мощным, чтобы приводить в движение несколько текстильных станков, и соответствующие станки приходилось размещать вокруг двигателя. Паровой двигатель также сделал возможным размещение производств не только у воды, а там, где были уголь, рабочие руки, рынки сбыта и транспорт. Новое время проводило и селекцию самых оптимальных конструкций зубчатых передач - тиражироваться начинали именно те, что давали максимальный экономический эффект. К середине ХIX века, по-видимому, следует отнести появление первых серийных редукторов. Ну а при появлении во второй половине XIX века электрического привода, бензиновых и дизельных двигателей означало разработку редукторов с заданными параметрами. Зубчатые механизмы предназначались для передачи вращательного движения от высокооборотных двигателей и преобразования (снижения) его параметров. Даже самые первые электродвигатели и ДВС обладали скоростью и моментом, как правило, не подходящим для использования в технологическом процессе.
Существует много разновидностей редукторов и классифицируются они по типу механических передач: цилиндрический, червячный, конической - цилиндрический.
2.4 Описание конструкции цилиндрического редуктора
Редуктор состоит из массивного чугунного корпуса, узлов зубчатых колес и шестерен с опорами, крышек подшипников и регулировочных колец (рисунок 2.2).
Рисунок 2.2 – Конструкция двухступенчатого цилиндрического
редуктора с развернутой схемой
КОРПУС служит для размещения в нем деталей передач, для заливки смазки зубчатых колес и подшипников, предохранения их от загрязнения и для восприятия усилий, возникающих в процессе работы механизма. Корпус должен быть достаточно прочным и жестким, так как в случае его деформации возникает перекос валов, что может привести к повышенному износу зубьев вследствие неравномерности распределения нагрузки и даже к поломке. Для повышения жесткости корпус усиливают ребрами, расположенными на участках размещения опор валов. Для удобства монтажа корпус выполнен разъемным. Плоскость разъема горизонтальна и проходит через оси валов. Нижняя часть корпуса 1 называется картером, верхняя 2 – крышкой. На крышке имеется смотровое окно 3, закрытое прямоугольной крышкой с отдушиной 4, которая служит для выравнивания давления внутри корпуса редуктора с атмосферным. В картере 1 имеется пробка 5 для слива масла и щуп 6 для замера его уровня. Картер и крышку скрепляют болтами 7, 8.
ЗУБЧАТЫЕ КОЛЕСА служат для передачи вращательного движения. В редукторе могут быть цилиндрические прямозубые или косозубые колеса. По сравнению с прямозубыми косозубые передачи имеют повышенную нагрузочную способность и работают более плавно.
Колеса 10, 11 насаживают на вал по посадке, гарантирующей натяг в сопряжении, или используют шпонки 12, 13. В отдельных случаях шестерни изготавливают заодно с валом, получая так называемые валы-шестерни.
ПОДШИПНИКИ
14, 15, 16 служат для поддержки вращающихся валов. Подшипник качения состоит из внутреннего и наружного колец с желобами для качения шариков, комплекта шариков (роликов) и сепаратора, удерживающего шарики (ролики) на
определенном расстоянии друг от друга. Подшипник надевают на вал неподвижно и вставляют в корпус по посадке с зазором.
КРЫШКИ ПОДШИПНИКОВ 17–21 служат для предотвращения попадания пыли и грязи внутрь корпуса и в подшипниковые узлы.
БОЛТОВЫЕ СОЕДИНЕНИЯ служат для скрепления корпуса и крышки редуктора.
ШТИФТЫ 9 предназначены для точного фиксирования положения крышки относительно корпуса редуктора при совместной расточке гнезд под подшипники и при сборке редуктора.
СМАЗКА РЕДУКТОРА в настоящее время в машиностроении широко применяется циркуляционная и картерная. В данной конструкции редуктора применена картерная смазка, которая осуществляется окунанием зубчатых колес в масло, заливаемое в картер редуктора. Смазка подшипников может быть густая (пластичная), и осуществляемая разбрызгиванием масла. Способ смазки выбирается с учетом окружной скорости зубчатых колес.
2.5 Порядок выполнения работы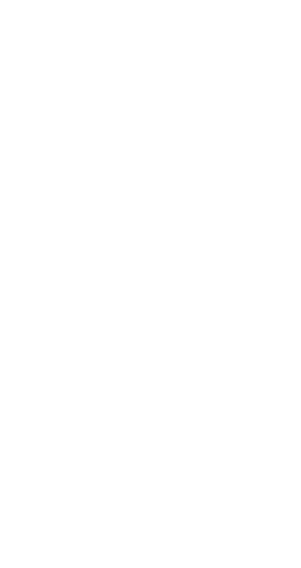
2.5.1
Разборка редуктора и ознакомление с конструкцией и назначением
отдельных узлов
Разборка одного из редукторов, указанных преподавателем, производится в следующем порядке: развинчивают болты крепления корпуса, поднимают крышку, используя отжимной болт. Поскольку крышка редуктора является тяжелой деталью, редуктор может перед началом работы находиться в разобранном виде, что дает возможность сразу приступить к знакомству с конструкцией и назначением деталей и узлов редуктора (валов, крышек, регулировочных колец, щупа масломера, сливной пробки).
2.5.2 Определение геометрических параметров быстроходной или тихоходной ступеней цилиндрического зубчатого редуктора
Для решения этой задачи необходимо провести ряд точных замеров с помощью штангенциркуля с точностью до 0,1 мм и вычислить параметры зацепления (рисунок 2.3). Для определения параметров каждой ступени редуктора необходимо сосчитать количество зубьев шестерни и колеса
каждой ступени, измерить диаметры вершин зубьев
, ширину колес , межосевые расстояния
, наружные диаметры подшипников
, внутренние диаметры подшипников
, ширину подшипников
.
Рисунок 2.3 – Основные геометрические параметры зубчатого зацепления
2.5.2.1
Модуль зубчатых колес –
основная характеристика размеров зубьев.Модуль – величина, пропорциональная шагу
по делительному цилиндру, измеренная в миллиметрах:
.
Для косозубых передач определяют торцовые и нормальные шаги и модули.
Шаг в торцовом сечении – это расстояние между одноименными точками профилей соседних зубьев, измеренное по дуге делительной окружности зубчатого колеса.
Нормальный шаг – кратчайшее расстояние по делительному цилиндру между одноименными точками двух соседних зубьев в сечении, перпендикулярном зубу:
,где
– угол наклона зубьев по делительному цилиндру. Соответственно, нормальный модуль:
.
Для прямозубых передач торцовые и нормальные шаги, и соответственно, модули совпадают. Модули стандартизированы (таблица 2.1).
Таблица 2.1 – Стандартные модули зубчатого зацепления
№ ряда | |
1; 1,25; 1,5; 2; 2,5; 3; 4; 5; 6; 8; 10; 12; 16; 20; 25 |
|
1; 1,25; 1,375; 1,75; 2,25; 2,75; 3,5; 4,5; 5,5; 5,7; 9; 11; 14; 18; 22 |
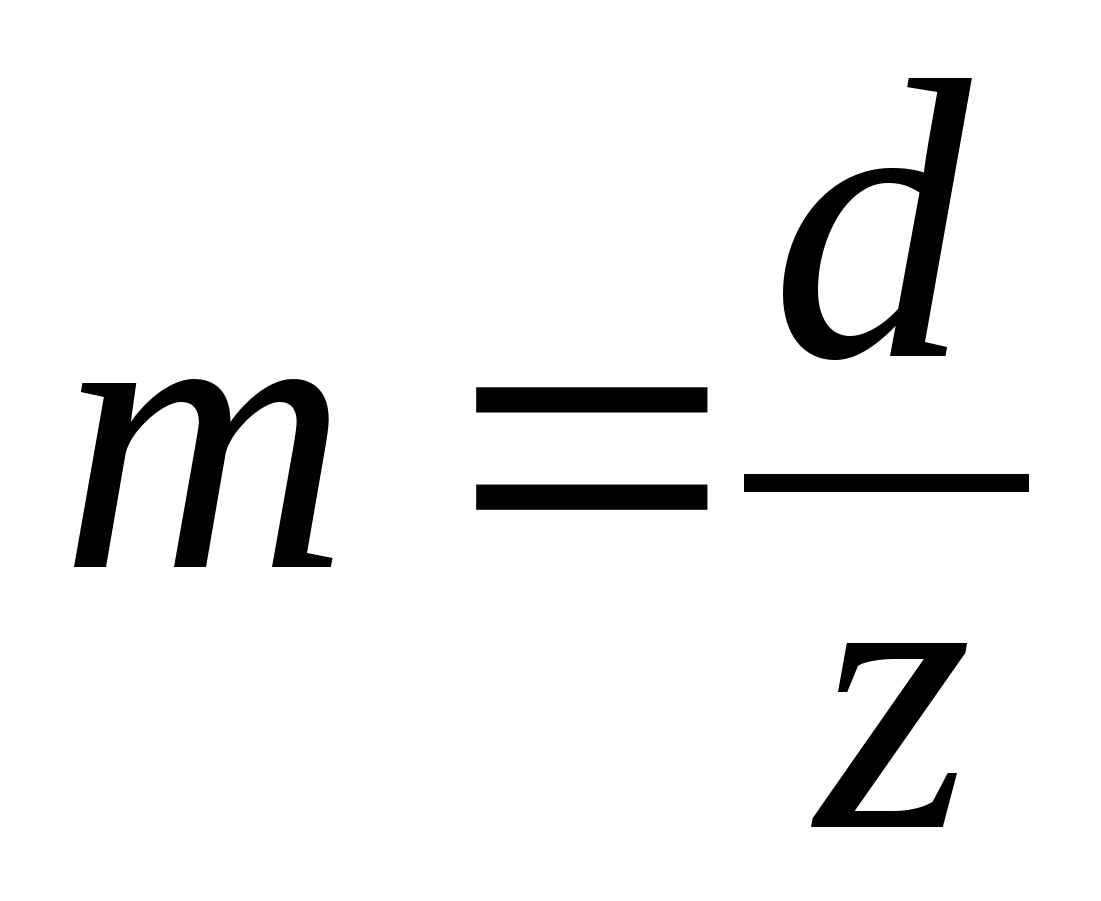
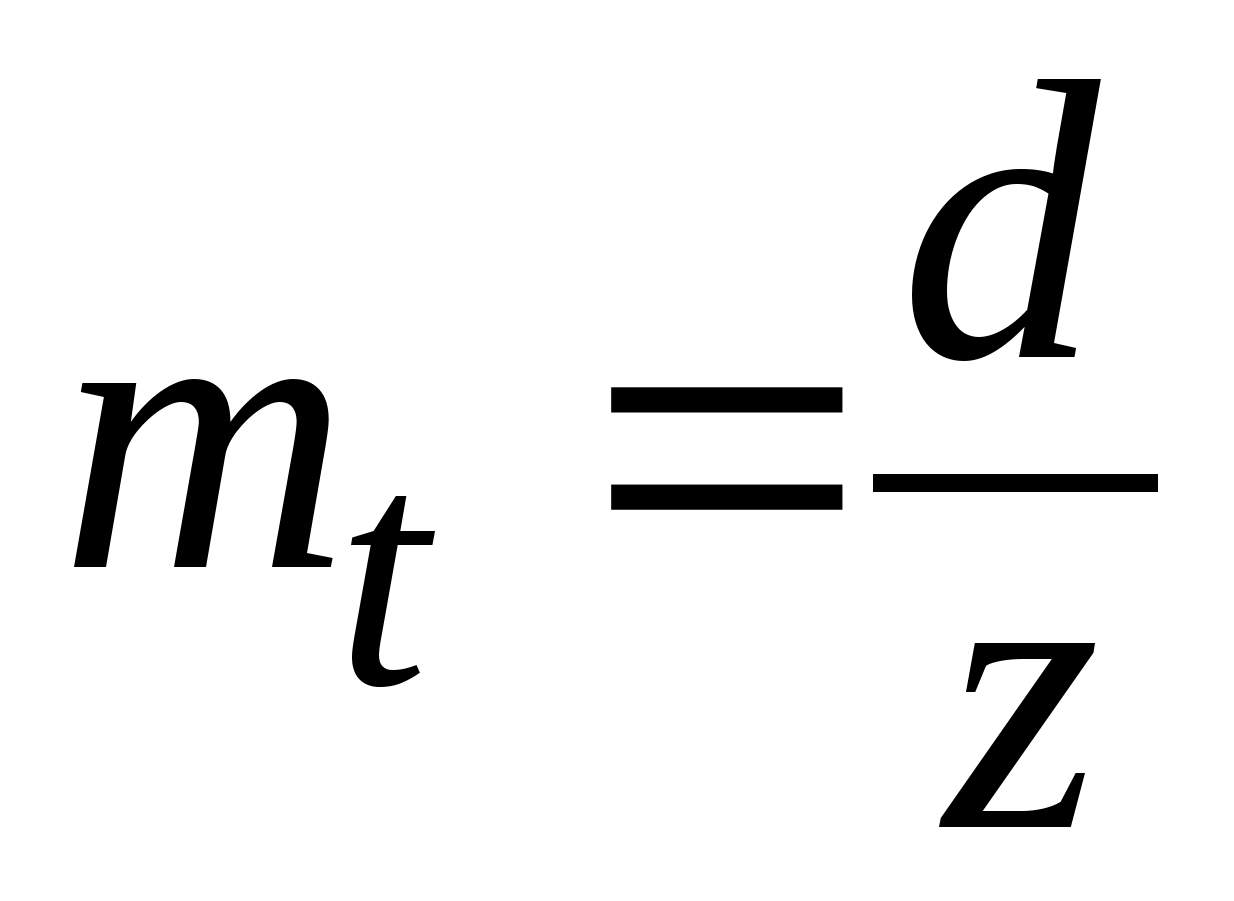
где
– делительный диаметр колеса, мм; – число зубьев.
Так как делительный диаметр колеса невозможно непосредственно замерить, то модуль колеса, а также некоторые его геометрические размеры, можно определить косвенно, пользуясь выражениями:
а) для прямозубых колес ,
;б) для косозубых колес
;в)
;г) h
=
2,25 m
,где
–
диаметр колеса по вершинам зубьев, мм;
–
диаметр колеса по впадинам зубьев, мм; h
–
высота зуба.2.5.2.2 Передаточное число зубчатой передачи –
отношение числа z
2 зубьев большего колеса к числу z
1 зубьев меньшего (шестерни)
.
Передаточное число редуктора равно произведению передаточных чисел всех его ступеней. Для двухступенчатого редуктора:
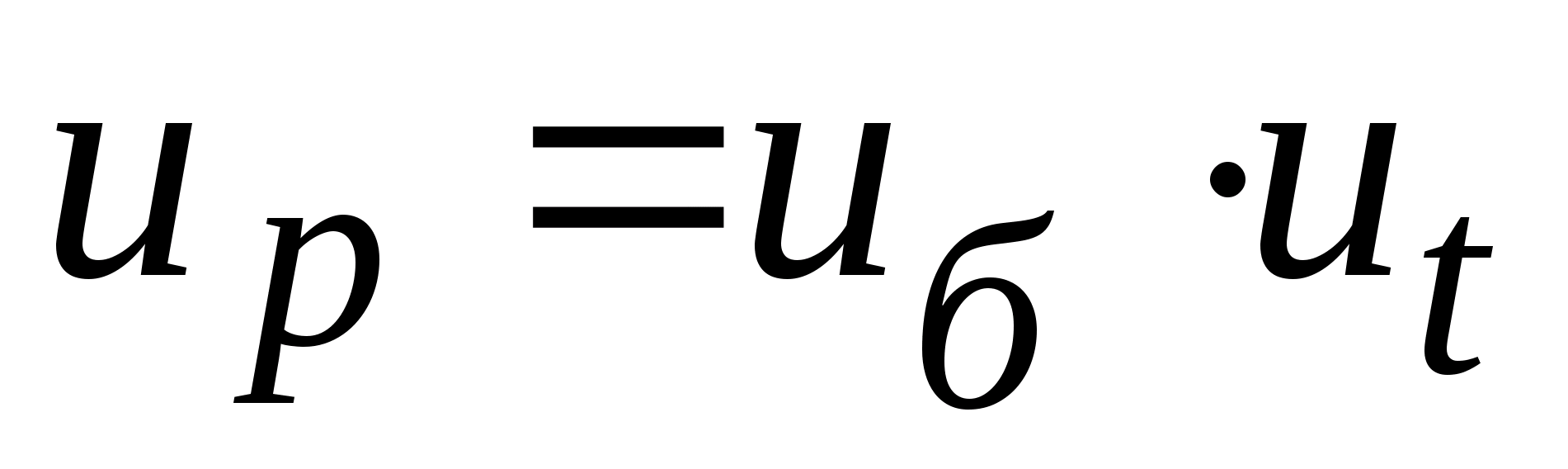
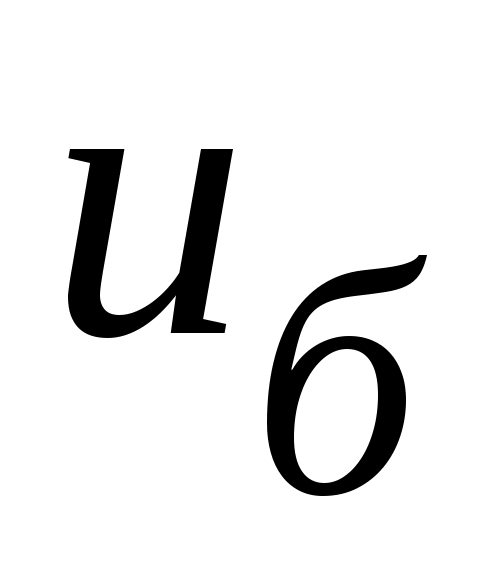
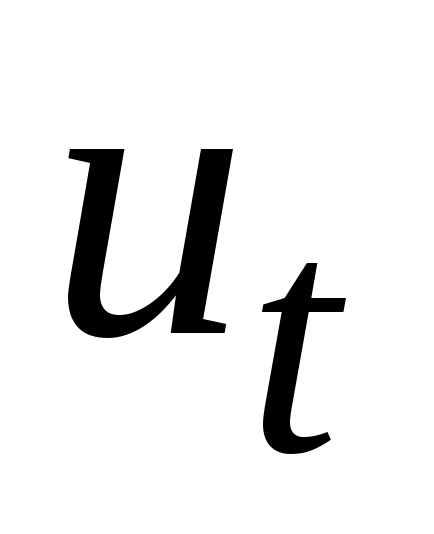
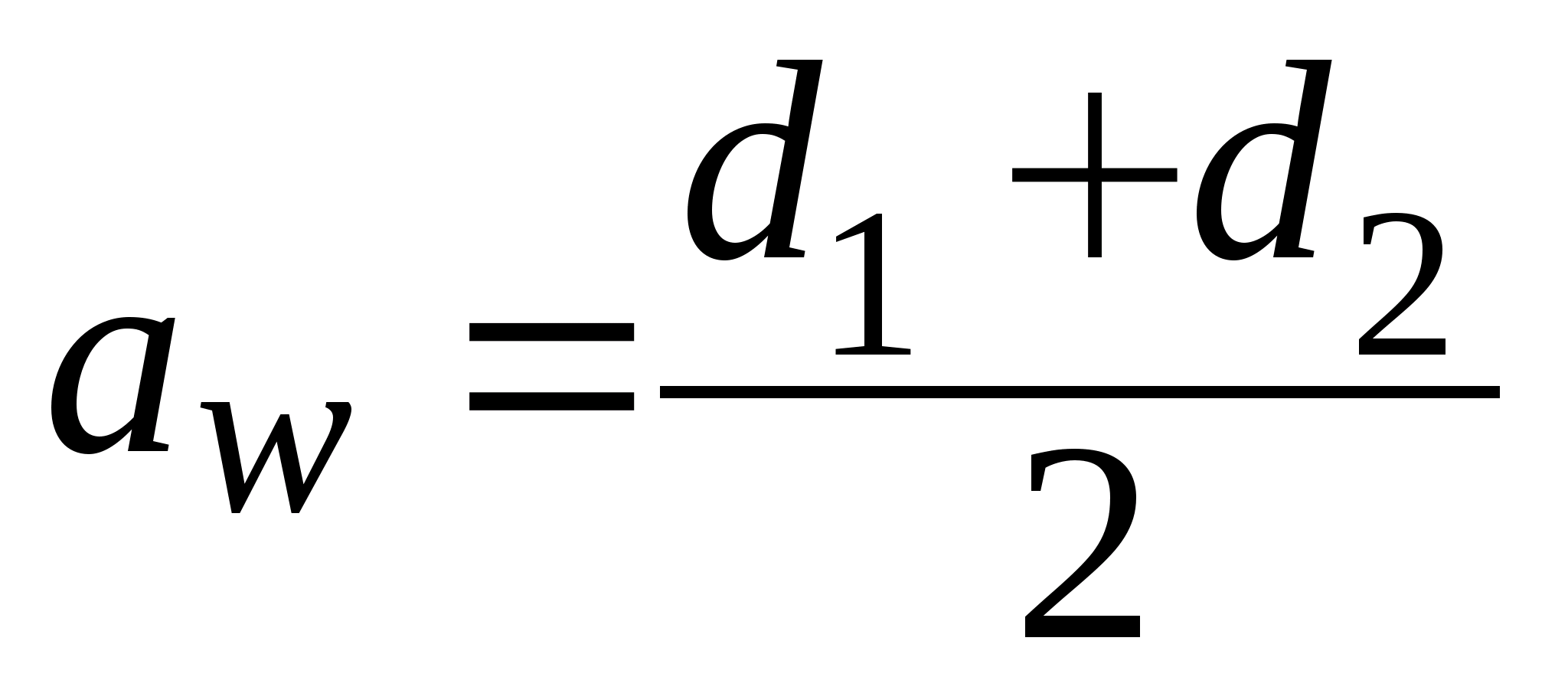
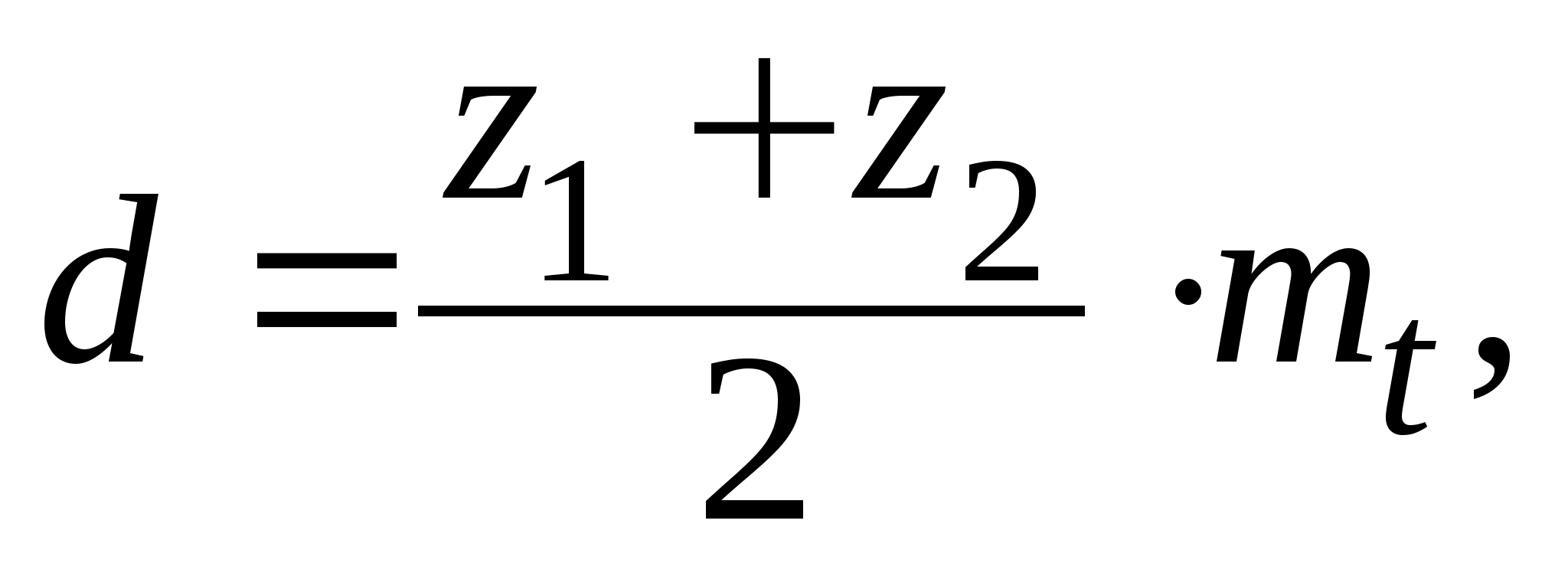
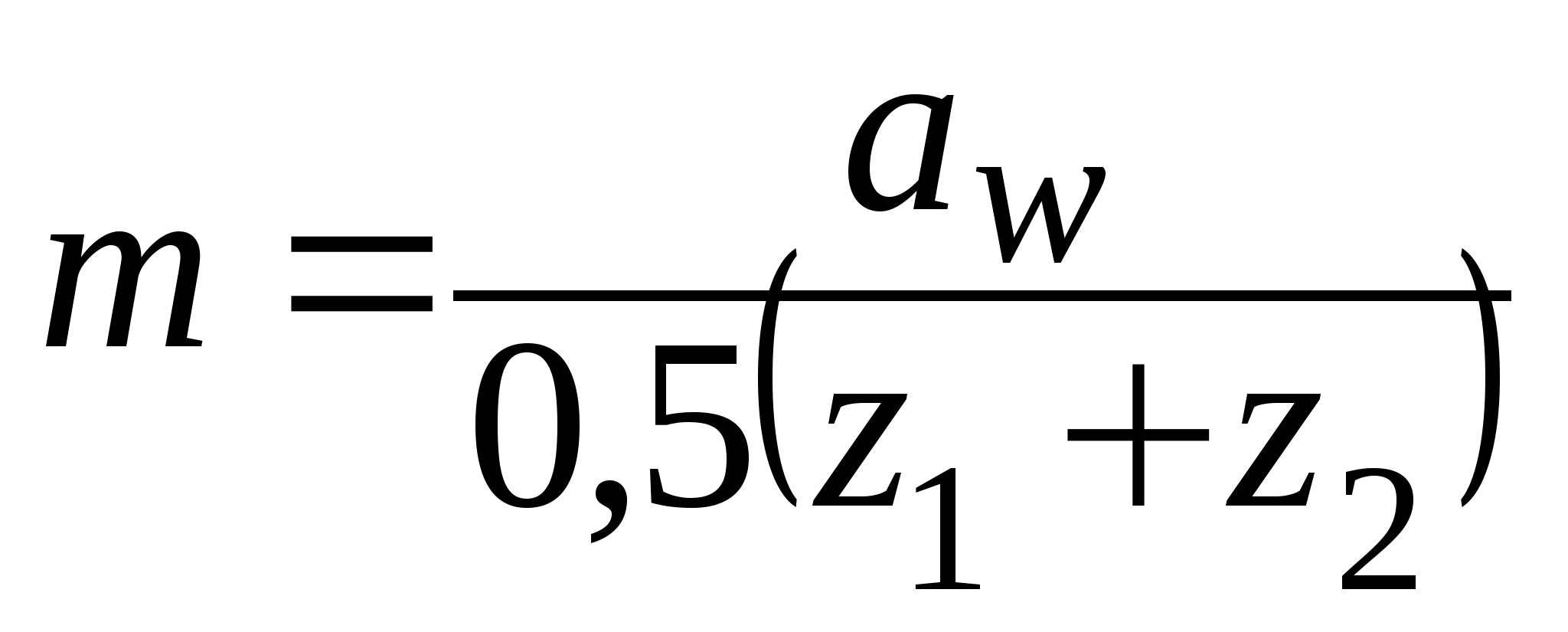
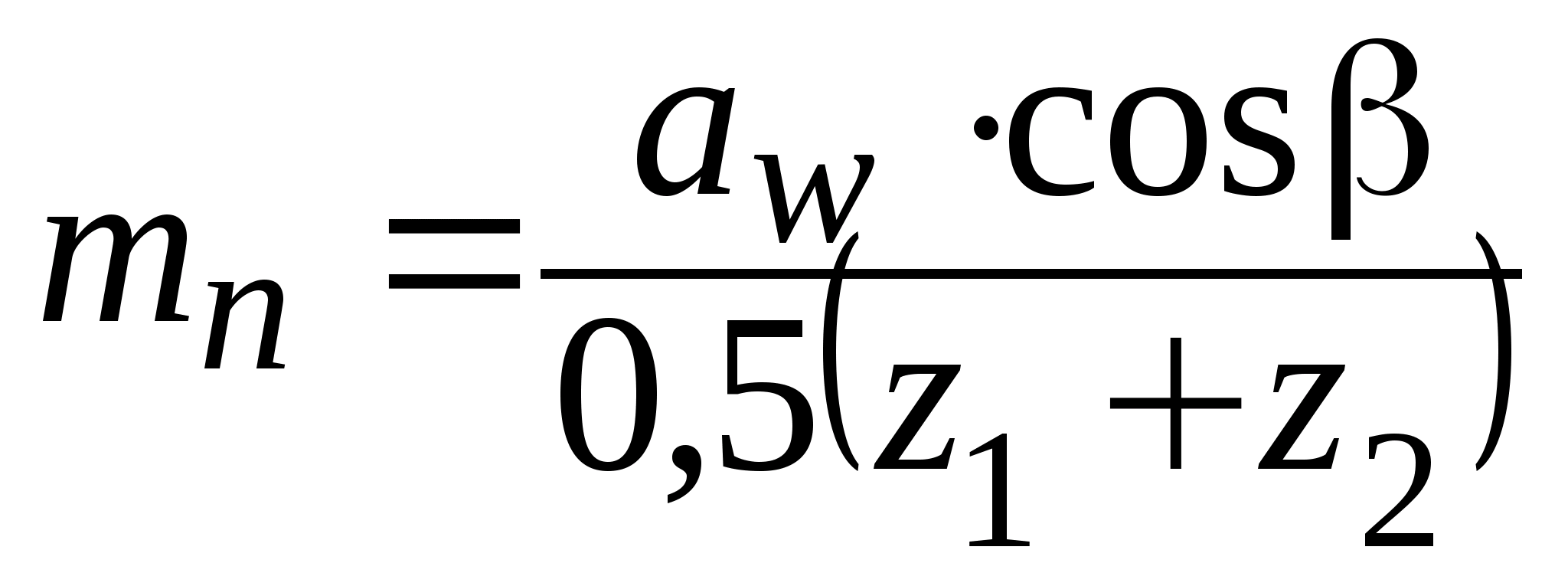
Так как угол в лабораторных условиях трудно определить достаточно точно, значение
может отличаться от стандартного значения. Приняв ближайшее стандартное значение модуля из таблицы 2.1, в обратном порядке рассчитывают фактическое значение угла (с точностью до секунд) и другие геометрические параметры передач. Результаты расчетов и измерений внести в таблицу 2.2.
Таблица 2.2 – Параметры зубчатого зацепления
Параметры | Быстроходная ступень | Тихоходная ступень |
Измерения: | ||
Количество зубьев | ||
Диаметр вершин зубьев ![]() | ||
Ширина колеса | ||
Межосевое расстояние ![]() | ||
Наружный диаметр подшипника | ||
Внутренний диаметр подшипника | ||
Ширина подшипника | ||
Расчетные значения: | ||
Передаточные числа ступеней, , ![]() | ||
Общее передаточное число редуктора ![]() | ||
Торцовый модуль ![]() | ||
Угол наклона | ||
Нормальный модуль ![]() | ||
Диаметры делительных окружностей колеса и шестерни | ||
Межосевое расстояние | ||
Высота h зуба |
д) выводы и заключения.
3 ЛАБОРАТОРНАЯ РАБОТА № 2.
ИССЛЕДОВАНИЕ
ХАРАКТЕРИСТИК РЕМЕННОЙ ПЕРЕДАЧИ
(4 часа)
Цель работы: экспериментальное определение зависимости ременной передачи от нагрузки (момента на ведомом шкиве), натяжения ремня, передаточного числа u .
Оборудование : специальная установка; штангенциркуль, линейка.
3.1 Общие сведения
Ременная передача относится к передачам трением с гибкой связью. Передача (рисунок 3.1) состоит из ведущего 1 и ведомого шкивов 2, огибаемых ремнем 3, натяжного устройства 4. Нагрузка передается силами трения, возникающими между шкивом и ремнем вследствие натяжения последнего. В зависимости от формы поперечного сечения ремня передачи бывают плоскоременные (рисунок 3.1б ), круглоременные (рисунок 3.1в ), клиновые (рисунок 3.1г ), поликлиновые (рисунок 3.1д ).
Рисунок 3.1 – Схема ременной передачи
Достоинства ременной передачи:
простота конструкции и малая стоимость;
Возможность передачи мощности на значительные расстояния;
плавность и бесшумность работы;
уменьшение вибрации из-за упругой вытяжки ремня.
Недостатки ременной передачи:
большие габариты;
малая долговечность ремня;
большие нагрузки на валы и опоры от натяжения ремня;
непостоянство передаточного отношения из-за упругого проскальзывания ремня.
Применяют ременную передачу в сочетании с другими передачами на быстроходных ступенях привода.
Передаваемая мощность – до 50 кВт, скорость ремня v = 5…50 м/с.
Основными геометрическими характеристиками (см. рисунок 3.1) ременных передач являются:
1) межосевое расстояние а ; впоследствии межосевое расстояние а уточняется при окончательно установленной длине ремня;
2) расчетная длина ремня l ;
3) угол обхвата ремнем малого шкива 1 .
3.1.1 Силы в передаче и напряжения в ремне
Для возникновения трения между ремнем и шкивом создают предварительное натяжение F 0 .
При приложении рабочей нагрузки Т 1 натяжение ведомой ветви снижается до величины F 2 , ведущей повышается до величины F 1 :
F 1 = F 0 + D F ; F 2 = F 0 – D F,
F 1 + F 2 = 2F 0 ;
окружная сила на шкиве:
F t = F 1 – F 2 .
Решая совместно два последних уравнения, получим:
F 1 = F 0 + F t / 2 ; F 2 = F 0 – F t / 2 .
При обегании ремнем шкивов в ремне возникает центробежная сила:
F v = rАv 2 ,
где А – площадь сечения, м 2 ; r – плотность материала, кг/м 3 ; v – скорость ремня, м/с.
Силы натяжения ветвей ремня нагружают валы и подшипники (рисунок 3.2а ).
Рисунок 3.2 – Силы в ветвях ремня: а ) T 1 <0; б ) T 1 >0
Равнодействующая сила F n = 2F 0 sin (a / 2).
Обычно величина F n в 2– 3 раза больше величины F t .
При работе ременной передачи от действующих сил возникают напряжения в материале ремня. Максимальное напряжение в ремне возникает в месте его набегания на малый шкив. Так как при перемещении ремня напряжение изменяется по величине, материал ремня со временем разрушается от усталости, здесь же возникают максимальные напряжения изгиба.
3.1.2 Скольжение ремня. Тяговая способность ременных передач
При передаче движения ремнем наблюдается проскальзывание ремня по поверхности шкива. Проскальзывание увеличивается с ростом нагрузки. В пределе может наступить пробуксовка ремня и передача движения прекратится.
Проскальзывание характеризуется коэффициентом проскальзывания E . При этом передаточное число:
u = 1 / 2 = d 1 / d 2 (1 - E ) ,
где 1 , 2 – угловая скорость вращения шкивов; d 1 , d 2 – диаметр шкивов.
Величина E зависит от нагрузки, угла обхвата ремнем шкива и от натяжения ремня.
3.2.1 Устройство и принцип работы установки
Основные элементы конструкции установки приведены на рисунке 3.3.
На литом основании 1 установки размещены: кронштейн 2 балансирной системы электродвигателя и подставка 15 с нагрузочным устройством. На кронштейне 2 балансирно в шарикоподшипниках установлен корпус электродвигателя 4.
На валу двигателя установлен ведущий двухступенчатый шкив 8.
Узел ведомого шкива смонтирован на подставке 15. В верхней части подставки в направляющих установлен ползун 20. В ползун вмонтирована ось, на которой шарнирно при помощи двух шарикоподшипников установлен корпус. К корпусу крепится нагрузочное устройство 10, вал которого сочленяется с валом двухступенчатого ведомого шкива 11. Вал ведомого шкива установлен в корпусе на двух шарикоподшипниках. К корпусу крепится рычаг 12, при нагружении которого создаётся момент вращения относительно оси, в результате чего корпус вместе с валом ведомого шкива может перемещаться в направлении от ведущего шкива, создавая тем самым дополнительное натяжение ремня.
При помощи ручки 13 производится перемещение ползуна 20 вместе с корпусом, за счет чего создаётся предварительный натяг ремня.
Ручкой 14 производится фиксация ползуна в направляющих при выбранном предварительном натяжении ремня. К валу нагрузочного устройства со стороны, противоположной ведомому шкиву, крепится рычаг, который своим концом создаёт усилие, приложенное к пружине. Величина деформации плоской пружины измеряется индикатором 27, установленным в кронштейне 9.
На валах ведущего и ведомого шкивов закреплены коллекторы контактных устройств. Сигналы, снимаемые с коллекторов контактных устройств, позволяют определить с помощью счётчиков 19 и 23 количество оборотов ведомого и ведущего валов. На панели 16 установлены: выключатель 26 общего питания установки, выключатель двигателя 25, регулятор скорости 24, счётчик оборотов ведущего вала 23, счётчик оборотов ведомого вала 19, выключатель цепей управления счётчиков 22, переключатель сигналов с контактных устройств 21 на счётчики, выключатель цепи возбуждения нагрузочного устройства 18 и регулятор тока возбуждения нагрузочного устройства 17.
На задней стороне основания прибора установлена клемма заземления и выведен кабель с вилкой на конце для подключения прибора к источнику питания.
Нагрузочное устройство представляет собой магнитный порошковый тормоз, принцип действия которого основан на свойстве намагниченной среды оказывать сопротивление перемещению в ней ферромагнитных тел.
В качестве намагниченной среды в конструкции применена жидкая смесь минерального масла и железного порошка.
Редуктор общемашиностроительного назначения. Этот тип оборудования представляет собой самостоятельный агрегат, используемый в приводах машин. Его технические характеристики отвечают общим для разных применений требованиям. Конструктивно общемашиностроительные редукторы могут отличаться.
Специальные редукторы разработаны для автомобильной, авиационной и других узкоспециализированных отраслей. Из названия понятно, что агрегаты этой группы должны соответствовать специфике и параметрам конкретного применения.
Редукторы можно классифицировать по следующим признакам:
- По типам передач и числу ступеней;
- По расположению осей входного/выходного валов в пространстве и относительно друг друга;
- По способу крепления.
1.1 Количество ступеней и расположение валов
У двух- и трехступенчатых редукторов развернутых и раздвоенных схем (в случае с двухступенчатыми моделями еще и соосных схем) есть ряд преимуществ перед агрегатами других типов – прежде всего это высокий КПД и устойчивость к нагрузкам. Соосные цилиндрические редукторы могут комплектоваться тихоходной ступенью с внутренним зацеплением. Планетарные и волновые агрегаты с соосным расположением осей валов также обеспечивают высокую производительность и широкий диапазон передаточных чисел.
При комплектации машин и механизмов, требующих пересекающегося расположения валов, будут эффективны двух- и трехступенчатые конические (коническо-цилиндрические) редукторы.
Агрегаты с червячными (червячно-цилиндрическими, цилиндрическо-червячными) передачами характеризуются высоким передаточным числом и низким уровнем шума. Однако КПД у таких моделей ниже, чем у цилиндрических аналогов.
Вертикальное расположение выходных валов требует меньшего пространства. В механизмах, где необходима подобная компоновка, чаще используются червячные или конические редукторы. Удобство заключается в том, что ось двигателя находится в горизонтальном положении.
Таблица 1. Классификация редукторов по расположению осей валов
Редуктор | Расположение осей |
---|---|
Параллельные оси входного/выходного валов |
1. Горизонтальное: - оси в горизонтальной плоскости; - оси в вертикальной плоскости (входной вал – над или под выходным валом); - оси в наклонной плоскости. 2. Вертикальное |
Совпадающие оси входного/ и выходного валов (соосный) |
1. Горизонтальное 2. Вертикальное |
Пересекающиеся оси входного/выходного валов |
1. Горизонтальное |
Скрещивающиеся оси входного/выходного валов |
1. Горизонтальное (входной вал – над или под выходным валом) 2. Горизонтальная ось входного вала и вертикальная ось выходного вала 3. Вертикальная ось входного вала и горизонтальная ось выходного вала |
1.2 Типы используемых передач
1.2.1 Червячные редукторы
Червячный редуктор – наиболее распространенный тип редукторов. Привод имеет компактные размеры (в сравнении с цилиндрическими агрегатами). Передаточное отношение червячной пары может достигать 1-100 (иногда и выше).
Потенциал увеличения крутящего момента при снижении частоты вращения вала у червячных редукторов выше, чем у оборудования с другими типами передач. Передаточное число того же порядка можно получить при эксплуатации трехступенчатого цилиндрического редуктора. В червячных агрегатах для решения этой задачи достаточно одной ступени. Еще одно преимущество – простота и низкая стоимость червячных редукторов. Использование червячного зацепления позволяет снизить уровень шума передачи, обеспечить высокую плавность хода.
Функция самоторможения присутствует только в червячных редукторах. Ее принцип основан на торможении ведомого вала при отсутствии движения на ведущем валу (червяке). Самоторможение в передаче осуществляется в тот момент, когда угол подъема ведущего вала меньше или равен 3,5 градусам.
При выборе червячного редуктора следует учитывать тот факт, что при увеличении передаточного числа снижается КПД червячной передачи. Отсюда – потери энергии вследствие трения червяка об зубья колеса.
Ресурс червячных приводов составляет, в среднем, 10 тысяч часов.
1.2.2 Червячный глобоидный редуктор
Винт глобоидного червячного редуктора имеет выпуклую форму (в других червячных передачах он цилиндрический). Эта конструктивная особенность увеличивает передачу крутящего момента и мощность привода.
Глобоидные редукторы предназначены для использования в условиях, предполагающих высокую надежность, отсутствие обратного проскальзывания и динамических толчков на выходном валу. Чаще всего редукторы этого типа применяются в барабанных приводах лифтов: глобоидная пара адаптирована к переменным нагрузкам, возникающим при подъеме и торможении кабины, в состоянии поддерживать нормальную реверсивность при эксплуатации.
Таблица 2. Допустимые нагрузки для червячных глобоидных редукторов типа ЧГ
Типоразмеры | Номинальное передаточное число | Частота вращения червяка, об/мин | |||||
---|---|---|---|---|---|---|---|
750 | 1000 | 1500 | |||||
Р вх, кВт | Т вых, Н м | Р вх, кВт | Т вых,Н·м | Р вх, кВт | Т вых, Н·м | ||
Чг-63 | 10 | 1,2 | 120 | 1,5 | - | 1,9 | 110 |
12,5 | 1,1 | 130 | 1,3 | 130 | 1,7 | 110 | |
16 | 1,0 | 150 | 1,2 | 150 | 1,5 | 130 | |
20 | 0,8 | 150 | 0,9 | 150 | 1,3 | 130 | |
25 | 0,5 | 125 | 0,6 | 110 | 0,8 | 110 | |
31,5 | 0,4 | 110 | 0,5 | 110 | 0,6 | 90 | |
40 | 0,3 | 110 | 0,3 | 100 | 0,5 | 90 | |
50 | 0,2 | 100 | 0,3 | 100 | 0,3 | 90 | |
63 | 0,1 | 90 | 0,2 | 90 | 0,3 | 80 | |
Чг-80 | 10 | 2,4 | 250 | 2,8 | 220 | 3,1 | 170 |
12,5 | 2,0 | 260 | 2,4 | 240 | 2,6 | 180 | |
16 | 1,6 | 260 | 1,9 | 240 | 2,1 | 180 | |
20 | 1,5 | 300 | 1,7 | 260 | 1,8 | 200 | |
25 | 1,0 | 250 | 1,1 | 220 | 1,5 | 190 | |
31,5 | 0,7 | 220 | 0,8 | 200 | 1,1 | 180 | |
40 | 0,6 | 220 | 0,7 | 200 | 0,9 | 180 | |
50 | 0,5 | 210 | 0,5 | 180 | 0,6 | 160 | |
63 | 0,3 | 200 | 0,4 | 170 | 0,5 | 150 | |
Чг-100 | 10 | 4,3 | 460 | 4,7 | 380 | 6,3 | 350 |
12,5 | 3,8 | 500 | 4,0 | 400 | 5,5 | 380 | |
16 | 3,0 | 500 | 3,6 | 450 | 4,6 | 400 | |
20 | 2,7 | 550 | 3,2 | 500 | 3,9 | 420 | |
25 | 2,0 | 500 | 2,3 | 450 | 3,0 | 400 | |
31,5 | 1,4 | 420 | 1,6 | 380 | 2,1 | 350 | |
40 | 1,2 | 420 | 1,3 | 380 | 1,8 | 350 | |
50 | 0,9 | 400 | 1,0 | 350 | 1,3 | 320 | |
63 | 0,7 | 380 | 0,8 | 320 | 1,1 | 300 | |
Чг-125 | 10 | 8,4 | 900 | 10,4 | 850 | 12,3 | 700 |
12,5 | 7,1 | 950 | 8,9 | 900 | 10,0 | 700 | |
16 | 5,6 | 950 | 7,0 | 900 | 8,5 | 750 | |
20 | 5,3 | 1100 | 6,3 | 1000 | 7,8 | 850 | |
25 | 4,0 | 1000 | 4,6 | 900 | 5,2 | 700 | |
31,5 | 2,9 | 900 | 3,4 | 800 | 3,9 | 650 | |
40 | 2,4 | 900 | 2,8 | 800 | 3,2 | 650 | |
50 | 1,7 | 800 | 2,1 | 750 | 2,6 | 650 | |
63 | 1,4 | 750 | 1,7 | 700 | 2,1 | 600 | |
Чг-160 | 10 | 16,7 | 1850 | 20,3 | 1700 | 28,3 | 1600 |
12,5 | 13,9 | 1900 | 16,3 | 1700 | 22,8 | 1600 | |
16 | 11,0 | 1900 | 13,7 | 1800 | 18,6 | 1650 | |
20 | 9,7 | 2050 | 11,9 | 1900 | 16,5 | 1800 | |
25 | 7,6 | 1950 | 8,6 | 1700 | 11,2 | 1500 | |
31,5 | 5,7 | 1800 | 6,4 | 1550 | 8,2 | 1350 | |
40 | 4,6 | 1800 | 5,1 | 1550 | 6,6 | 1350 | |
50 | 3,6 | 1650 | 4,0 | 1450 | 5,0 | 1250 | |
63 | 2,8 | 1550 | 3,4 | 1450 | 4,1 | 1200 |